Table of Contents:
- Introduction to Custom Sheet Metal Fabrication
- The Advantages of Custom Sheet Metal Fabrication
- The Materials Used in Custom Sheet Metal Fabrication
- The Techniques Used in Custom Sheet Metal Fabrication
- The Applications of Custom Sheet Metal Fabrication
- The Benefits of Choosing a Professional Custom Sheet Metal Fabricator
- The Process of Custom Sheet Metal Fabrication
- Common Types of Custom Sheet Metal Products
- Choosing the Right Custom Sheet Metal Fabrication Company
- Conclusion: Why Custom Sheet Metal Fabrication is a Great Choice for Your Business
-
1.Introduction to Custom Sheet Metal Fabrication
Custom sheet metal fabrication is a manufacturing process that involves shaping and forming sheet metal into custom-designed parts and products. Sheet metal is a versatile material that can be cut, bent, and formed into a wide range of shapes and sizes, making it an ideal choice for a variety of applications. From small components to large structures, sheet metal fabrication can create products with precise specifications and dimensions.
Custom sheet metal fabrication is used in a range of industries, including aerospace, automotive, construction, and electronics. It can be used to create everything from simple brackets and enclosures to complex assemblies and structures. The process typically involves using specialized tools and equipment, such as laser cutters, press brakes, and welding machines, to cut, form, and join sheet metal parts.
In this guide, we will explore the advantages of custom sheet metal fabrication, the materials and techniques used in the process, the applications and benefits of choosing a professional fabricator, the process itself, common types of products produced, and how to choose the right custom sheet metal fabrication company for your needs.
-
2.The Advantages of Custom Sheet Metal Fabrication
Custom sheet metal fabrication offers a number of advantages over other manufacturing processes. Here are some of the key advantages:
- Customization: One of the biggest advantages of custom sheet metal fabrication is the ability to create products that are tailored to specific requirements. This means that the product can be designed to fit a specific space, perform a particular function, or meet certain aesthetic requirements.
- Precision: Sheet metal fabrication allows for precise control over the size, shape, and dimensions of the product. This precision ensures that the product will fit and function as intended, without the need for additional modifications.
- Strength and durability: Sheet metal is a strong and durable material that can withstand harsh environments and heavy use. By using the right techniques and materials, sheet metal fabricators can produce products that are both strong and durable.
- Versatility: Sheet metal can be formed into a wide range of shapes and sizes, making it a versatile material for a variety of applications. This versatility makes it a popular choice in many industries, from automotive to aerospace.
- Cost-effective: Custom sheet metal fabrication can be a cost-effective manufacturing process, especially for large production runs. The process can also reduce the need for additional components or materials, as the sheet metal can be formed into a single part.
- Quick turnaround: Sheet metal fabrication can be a fast process, with many products being produced in a matter of days. This makes it a popular choice for businesses that need to quickly produce large quantities of products.
-
3.The Materials Used in Custom Sheet Metal Fabrication
Custom sheet metal fabrication can be done using a variety of materials, depending on the specific requirements of the product being produced. Here are some of the most commonly used materials in custom sheet metal fabrication:
- Steel: Steel is a popular choice for sheet metal fabrication because it is strong and durable. It can be formed into a wide range of shapes and sizes and is commonly used in the construction, automotive, and aerospace industries.
- Aluminum: Aluminum is a lightweight material that is also strong and durable. It is commonly used in the aerospace and automotive industries because of its high strength-to-weight ratio.
- Stainless steel: Stainless steel is a corrosion-resistant material that is commonly used in environments where corrosion is a concern. It is often used in the food processing, medical, and pharmaceutical industries.
- Copper: Copper is a good conductor of heat and electricity, making it a popular choice for electrical components. It is also used in the construction and plumbing industries.
- Brass: Brass is an alloy of copper and zinc and is often used for decorative purposes because of its attractive appearance. It is also commonly used in the manufacturing of valves, locks, and musical instruments.
- Titanium: Titanium is a lightweight and strong material that is commonly used in the aerospace and medical industries. It is also corrosion-resistant and has a high strength-to-weight ratio.
-
4.The Techniques Used in Custom Sheet Metal Fabrication
Custom sheet metal fabrication involves a range of techniques to cut, bend, form, and join sheet metal into the desired shape and size. Here are some of the most commonly used techniques in sheet metal fabrication:
- Cutting: Cutting is the first step in the sheet metal fabrication process. It involves using specialized tools such as shears, laser cutters, or waterjets to cut the sheet metal to the desired size and shape.
- Bending: Bending is the process of using a press brake or other bending tools to bend the sheet metal into the desired shape. This is done by applying pressure to the sheet metal, which causes it to bend at a specific angle.
- Forming: Forming is the process of shaping the sheet metal into a specific shape or contour. This can be done by using a variety of tools, such as rollers or stamping presses.
- Welding: Welding is the process of joining two pieces of sheet metal together by heating them to a high temperature and fusing them together. This can be done using various welding techniques, such as MIG, TIG, or spot welding.
- Assembly: Assembly is the process of joining multiple sheet metal components together to create a finished product. This can involve welding, riveting, or using adhesives to join the components.
- Finishing: Finishing is the final step in the sheet metal fabrication process. It involves cleaning, smoothing, and polishing the surface of the sheet metal to improve its appearance and protect it from corrosion.
-
5.The Applications of Custom Sheet Metal Fabrication
Custom sheet metal fabrication can be used in a wide range of applications across a variety of industries. Here are some of the most common applications of custom sheet metal fabrication:
- Automotive industry: Custom sheet metal fabrication is used in the manufacturing of cars, trucks, and other vehicles. Sheet metal is used for body panels, frames, and other structural components.
- Aerospace industry: Sheet metal fabrication is used in the manufacturing of aircraft, spacecraft, and other aerospace vehicles. Sheet metal is used for components such as wings, fuselages, and engine parts.
- Construction industry: Custom sheet metal fabrication is used in the construction of buildings, bridges, and other structures. Sheet metal is used for roofing, siding, and structural components.
- Medical industry: Custom sheet metal fabrication is used in the manufacturing of medical equipment and devices. Sheet metal is used for components such as surgical instruments, medical carts, and patient tables.
- Electronics industry: Custom sheet metal fabrication is used in the manufacturing of electronic enclosures, racks, and cabinets. Sheet metal is used to create custom shapes and sizes to fit specific electronic components.
- Food and beverage industry: Custom sheet metal fabrication is used in the manufacturing of food processing equipment, such as mixers, conveyors, and tanks. Sheet metal is used because it is easy to clean and resistant to corrosion.
- Energy industry: Custom sheet metal fabrication is used in the manufacturing of energy equipment, such as wind turbines, solar panels, and power generators. Sheet metal is used for components such as frames, housings, and enclosures.
-
6.The Benefits of Choosing a Professional Custom Sheet Metal Fabricator
Choosing a professional custom sheet metal fabricator for your project can provide several benefits, including:
- Expertise and experience: A professional sheet metal fabricator will have the knowledge, skills, and experience to design, manufacture, and finish sheet metal parts and components to the highest standards. They can provide expert advice on the best materials, techniques, and finishes to use for your project.
- Quality and precision: A professional sheet metal fabricator will use advanced tools and equipment to ensure that your parts and components are manufactured to precise specifications. They will have quality control procedures in place to ensure that your project is delivered on time and to the highest standards.
- Customization and flexibility: A professional sheet metal fabricator can provide custom solutions tailored to your specific needs. They can create parts and components in a wide range of sizes, shapes, and materials, to meet your unique requirements.
- Cost-effectiveness: A professional sheet metal fabricator can help you save money by reducing material waste, improving production efficiency, and minimizing the risk of errors or defects. They can also help you identify ways to optimize your design for manufacturing, which can help you reduce costs and improve quality.
- Customer service and support: A professional sheet metal fabricator will provide excellent customer service and support throughout your project. They will keep you informed of progress, answer your questions, and provide ongoing support and maintenance as needed.
-
7.The Process of Custom Sheet Metal Fabrication
A. Design and Planning: The first step in custom sheet metal fabrication is to create a design and plan for the project. This includes determining the required specifications, dimensions, and tolerances, as well as selecting the appropriate materials and finishes. The design and planning phase also involves creating detailed drawings or 3D models of the parts or components to be fabricated.
B. Material Selection: Once the design and planning phase is complete, the next step is to select the appropriate materials for the project. This includes choosing the type of sheet metal, such as steel, aluminum, or copper, as well as the thickness and grade of the material.
C. Cutting and Forming: The selected sheet metal is then cut and formed into the desired shape using specialized tools and equipment. This may involve processes such as laser cutting, punching, bending, and rolling, depending on the specific requirements of the project.
D. Welding and Assembly: Once the sheet metal parts and components have been cut and formed, they are welded and assembled together using various techniques, such as TIG or MIG welding. This may involve joining multiple pieces of sheet metal to create a larger structure or assembly.
E. Finishing and Quality Control: The final step in custom sheet metal fabrication is to apply any necessary finishes or coatings, such as paint or powder coating, to protect the metal from corrosion or other forms of damage. Quality control checks are also performed to ensure that the finished product meets all required specifications and standards.
-
8.Common Types of Custom Sheet Metal Products
Custom sheet metal fabrication can produce a wide range of products, depending on the specific needs and requirements of the customer. Here are some of the most common types of custom sheet metal products:
A. Metal Cabinets and Enclosures: Custom sheet metal fabrication can be used to produce cabinets and enclosures for a range of industries, including electronics, telecommunications, and manufacturing. These cabinets and enclosures can be designed to fit specific components and equipment, and can be made to any size or shape.
B. HVAC Components: Custom sheet metal fabrication can produce HVAC components such as ductwork, vents, and air handling units. These components are typically made from galvanized steel or aluminum to resist corrosion and withstand high temperatures.
C. Metal Brackets and Mounting Hardware: Custom sheet metal fabrication can produce a range of brackets and mounting hardware for various applications, such as electrical panels, medical equipment, and vehicle components. These brackets and hardware can be made to any size or shape, and are designed to provide secure and stable support for other components.
D. Signage and Displays: Custom sheet metal fabrication is often used to produce signage and displays for businesses and organizations. These can be made from various metals, such as aluminum or stainless steel, and can be designed to any size or shape. Custom finishes and coatings can also be added to enhance the appearance and durability of the signage and displays.
-
9.Choosing the Right Custom Sheet Metal Fabrication Company
Choosing the right custom sheet metal fabrication company is an important decision that requires careful consideration. Here are some factors to consider and questions to ask when selecting a custom sheet metal fabricator:
A. Factors to Consider:
- Expertise and experience: Look for a custom sheet metal fabricator that has the knowledge, skills, and experience to manufacture your parts or components to the highest standards.
- Quality and precision: Look for a custom sheet metal fabricator that has a reputation for producing high-quality and precision-engineered parts or components.
- Flexibility and customization: Look for a custom sheet metal fabricator that can provide custom solutions tailored to your specific needs, including the ability to work with a range of materials, sizes, and shapes.
- Equipment and technology: Look for a custom sheet metal fabricator that has the latest and most advanced tools and equipment to ensure the highest level of quality and precision.
- Customer service and support: Look for a custom sheet metal fabricator that provides excellent customer service and support throughout the fabrication process, and beyond.
B. Questions to Ask:
- Can you provide examples of similar projects you have completed in the past?
- What materials do you work with, and what types of finishes and coatings can you apply?
- What equipment and technology do you use for cutting, forming, and welding?
- What is your quality control process, and how do you ensure precision and accuracy in your fabrication work?
- What is your lead time for completing a custom sheet metal fabrication project?
- What is your pricing structure, and what factors affect the final cost of a project?
- What types of customer support and maintenance do you offer after the project is completed?
Click on the V1 Prototype website to gain more Sheet Metal Services information.
-
10.Conclusion: Why Custom Sheet Metal Fabrication is a Great Choice for Your Business
Custom sheet metal fabrication is an excellent choice for businesses that require precision-engineered parts and components to meet their specific needs and requirements. By working with a professional sheet metal fabricator, businesses can enjoy the following benefits:
- Customization and flexibility: Custom sheet metal fabrication provides businesses with the flexibility to create parts and components that are tailored to their specific needs, including size, shape, and material.
- Improved quality and precision: Custom sheet metal fabrication ensures that parts and components are manufactured to the highest standards, with advanced equipment and quality control procedures to ensure precision and accuracy.
- Cost-effectiveness: Custom sheet metal fabrication can help businesses save money by reducing material waste, improving production efficiency, and minimizing the risk of errors or defects.
- Durability and reliability: Custom sheet metal parts and components are durable, reliable, and resistant to corrosion, making them suitable for a wide range of applications across a variety of industries.
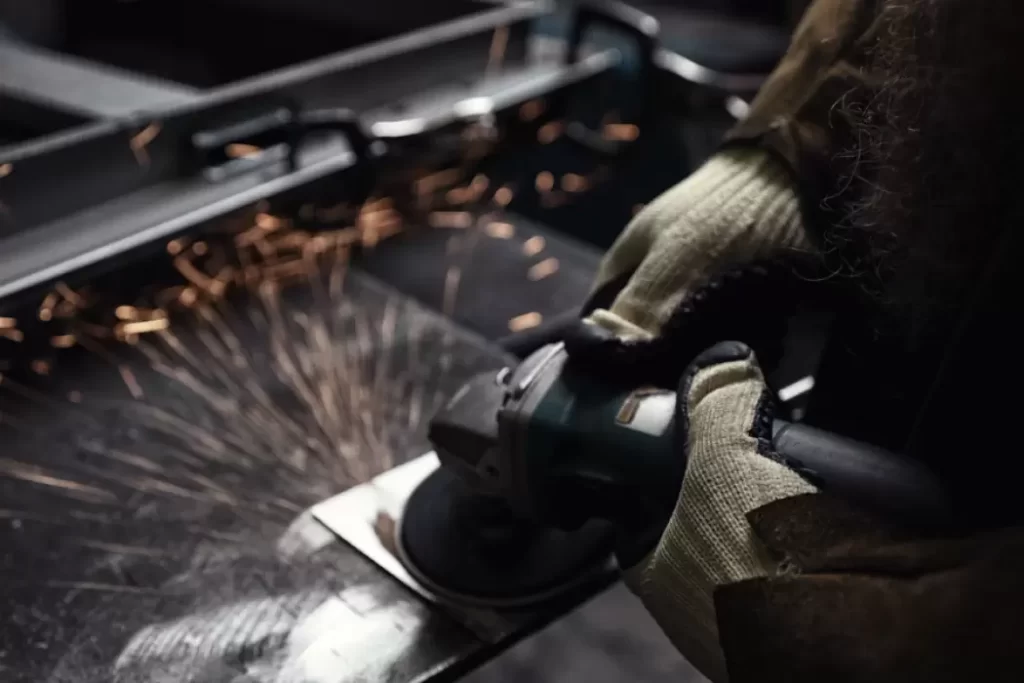
Overall, custom sheet metal fabrication offers businesses the opportunity to improve their manufacturing process, achieve their goals, and succeed in today’s competitive marketplace. By working with a professional sheet metal fabricator, businesses can enjoy the benefits of high-quality, precision-engineered parts and components that meet their specific needs, while also benefiting from the expertise and experience of a skilled fabrication team.
Sheet metal fabrication is the process of transforming flat sheets of metal into customized shapes and sizes for various purposes. It involves cutting, bending, welding, and finishing the metal using specialized tools and equipment. Custom sheet metal fabrication offers many benefits for businesses that need high-quality, durable, and versatile products. Some of these benefits are:
- Cost-effectiveness: Custom sheet metal fabrication can reduce material waste and labor costs by producing products that fit the exact specifications and requirements of the customers. It can also lower the maintenance and repair costs by ensuring the products are resistant to corrosion, wear, and tear.
- Flexibility: Custom sheet metal fabrication can create products that suit different applications and industries, such as aerospace, automotive, construction, medical, and more. It can also accommodate complex designs and shapes that are not possible with standard fabrication methods.
- Performance: Custom sheet metal fabrication can enhance the functionality and efficiency of the products by using high-quality materials and techniques. It can also improve the aesthetic appeal and durability of the products by applying various finishes and coatings.
However, not all sheet metal fabricators are created equal. To ensure the best results for your business, you need to choose a professional fabricator that has the following qualities:
- Experience: A professional fabricator should have extensive experience in custom sheet metal fabrication and be familiar with the industry standards and regulations. They should also have a portfolio of previous projects that demonstrate their skills and capabilities.
- Equipment: A professional fabricator should have access to the latest technology and equipment for custom sheet metal fabrication. They should also have a well-equipped facility that can handle large-scale and complex projects.
- Quality: A professional fabricator should adhere to strict quality control measures and ensure that the products meet or exceed the expectations of the customers. They should also offer warranties and guarantees for their products and services.
- Customer service: A professional fabricator should provide excellent customer service and communication throughout the fabrication process. They should also offer competitive pricing, timely delivery, and after-sales support.
If you are looking for a professional fabricator for your custom sheet metal fabrication needs, look no further than ABC Metalworks. We have over 20 years of experience in custom sheet metal fabrication and we can handle any project, big or small. We use high-quality materials and state-of-the-art equipment to create products that are tailored to your specifications and requirements. We also offer free estimates, fast turnaround times, and exceptional customer service. Contact us today to get started on your custom sheet metal fabrication project.