Introduction: The Future of Automotive Manufacturing
In recent years, the automotive industry has been witnessing a remarkable technological revolution. One technology that has been making significant strides in this domain is 3D printing. Known for its versatility and efficiency, 3D printing, also referred to as additive manufacturing, has been disrupting traditional manufacturing processes. Embracing this innovation, Volkswagen, one of the world's leading automakers, is taking a bold step towards the future by announcing its plans to expand production of cars using 3D printing. This move marks a pivotal moment in the history of automotive manufacturing, where advanced technology and cutting-edge design converge to shape the cars of tomorrow.
The Power of 3D Printing: A Paradigm Shift in Manufacturing
The incorporation of 3D printing in the automotive industry heralds a paradigm shift in the way cars are manufactured. Traditionally, automobile parts were fabricated using subtractive manufacturing methods, where materials were carved and shaped from a larger block. This approach was not only time-consuming but also generated a significant amount of material waste. In stark contrast, 3D printing is an additive process where complex parts are built layer by layer, reducing waste and material costs substantially. The ability to create intricate and customized components with 3D printing has opened up new horizons for Volkswagen to enhance their vehicle designs and optimize performance.
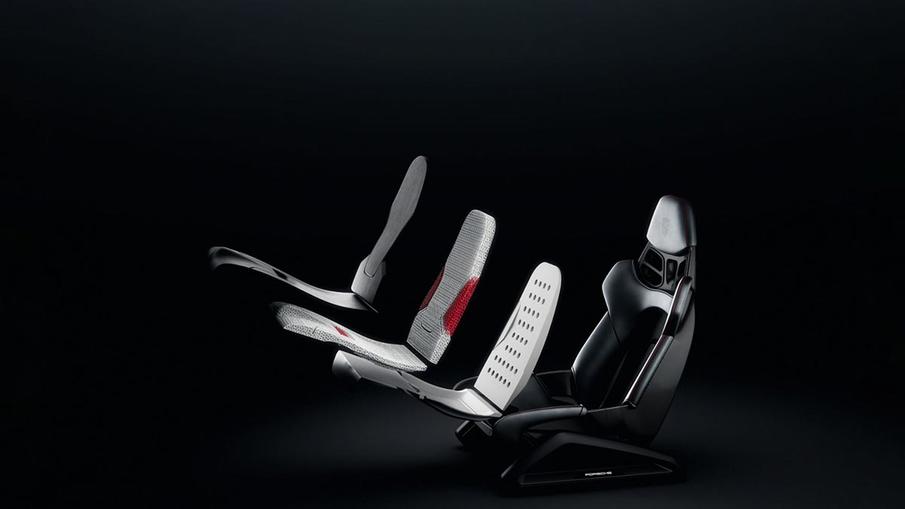
Volkswagen's Journey with 3D Printing: From Prototyping to Production
Volkswagen's venture into 3D printing is not entirely new. Like many other automotive giants, Volkswagen initially adopted 3D printing for rapid prototyping. This application enabled engineers and designers to iterate and refine their concepts swiftly, accelerating the development process. With advancements in additive manufacturing technologies and the growing confidence in its reliability, Volkswagen gradually expanded the use of 3D printing to produce specialized components, such as lightweight and durable engine parts and intricate interior elements.
The Promise of Customization and Personalization
One of the most exciting prospects of 3D printing in car production is the unprecedented level of customization and personalization it offers. Each car could potentially be tailored to meet the unique preferences and needs of its owner. Customers will have the opportunity to select from a wide array of design options, materials, and finishes, making their vehicles truly one-of-a-kind. Volkswagen's embrace of 3D printing signifies the automaker's commitment to providing a customer-centric approach, fostering stronger connections between drivers and their cars.
Environmental Impact: Sustainability and Reduced Carbon Footprint
Beyond its efficiency and customization capabilities, 3D printing aligns with Volkswagen's commitment to sustainability and environmental stewardship. The additive manufacturing process consumes fewer raw materials and reduces energy consumption compared to conventional manufacturing methods. By minimizing waste and optimizing material usage, Volkswagen aims to significantly reduce its carbon footprint throughout the production process. As consumers increasingly prioritize environmentally responsible products, Volkswagen's adoption of 3D printing sets a new standard for sustainable practices in the automotive industry.
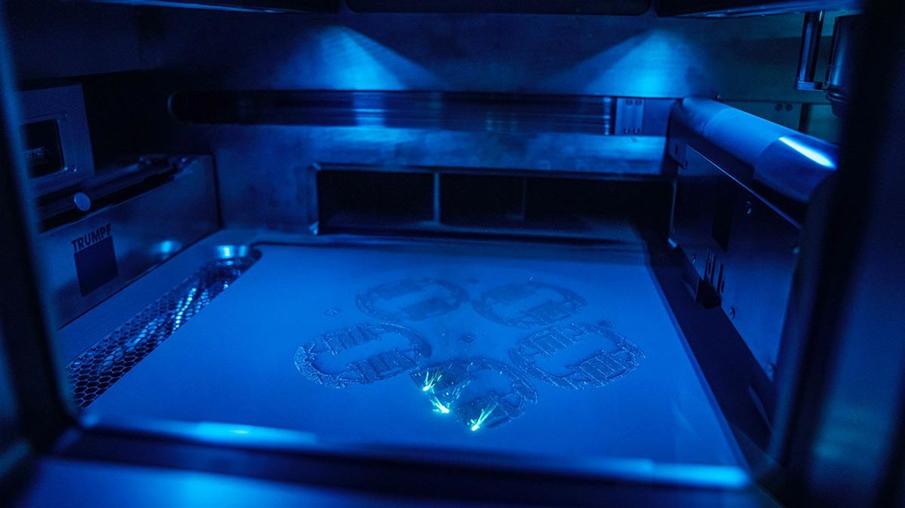
- How does 3D printing benefit Volkswagen's production process?
3D printing offers a myriad of benefits to Volkswagen's production process. Firstly, the technology streamlines prototyping, significantly reducing development time and costs. Rapid prototyping enables engineers to test and refine various design iterations efficiently. This iterative approach allows Volkswagen to deliver safer and more reliable vehicles to the market faster.
Additionally, 3D printing facilitates the production of complex geometries and lightweight components, improving vehicle performance and fuel efficiency. By using 3D printing to manufacture engine parts, Volkswagen can achieve higher power-to-weight ratios, leading to enhanced overall vehicle performance. Moreover, the ability to produce intricate interior components offers a unique opportunity to create comfortable and aesthetically pleasing cabin environments, enhancing the overall driving experience.
- What challenges might Volkswagen face in integrating 3D printing on a larger scale?
While 3D printing brings immense potential, there are challenges that Volkswagen must address when expanding its usage on a larger scale. One significant hurdle is the scalability of the technology. Producing cars using 3D printing may not be as fast as traditional assembly lines, especially for larger components. To achieve high-volume production, Volkswagen must invest in state-of-the-art 3D printing facilities and optimize the manufacturing process for efficiency.
Another concern is the choice of materials. While 3D printing allows for various materials to be used, ensuring their durability and safety for automotive applications requires rigorous testing and compliance with industry standards. Finding the right balance between innovative materials and safety standards will be crucial for Volkswagen to maintain the highest level of quality and reliability in their vehicles.
- How will the expansion of 3D printing affect the affordability of Volkswagen cars?
Initially, the integration of 3D printing might not significantly impact the affordability of Volkswagen cars, given the current high costs associated with the technology and the development of new materials. However, as 3D printing technology matures, becomes more widespread, and economies of scale come into play, production costs are likely to decrease. This cost reduction could eventually translate into more affordable vehicles for consumers. Additionally, 3D printing's ability to optimize vehicle designs may lead to increased fuel efficiency, potentially offsetting any initial cost increase.
- What implications does 3D printing have on the automotive industry as a whole?
The widespread adoption of 3D printing in automotive manufacturing will reverberate throughout the industry in various ways. Firstly, it will foster a shift towards more localized production, as 3D printing allows for on-demand manufacturing and decentralized supply chains. This decentralization could reduce transportation-related emissions and logistical complexities.
Furthermore, 3D printing may democratize car design and production, opening up opportunities for smaller companies and startups to enter the market. With lower entry barriers and customizable designs, niche markets and specialized vehicles might become more feasible.
In conclusion, Volkswagen's commitment to expanding the use of 3D printing in car production represents a pivotal moment for the automotive industry. With the promise of increased efficiency, customization, sustainability, and performance, 3D printing has the potential to redefine how cars are made and experienced. As the technology continues to evolve and become more accessible, we can expect to see a transformative shift in the way cars are designed, manufactured, and cherished by customers worldwide. The road ahead looks thrilling and promising, as the automotive industry accelerates towards a more innovative and sustainable future.
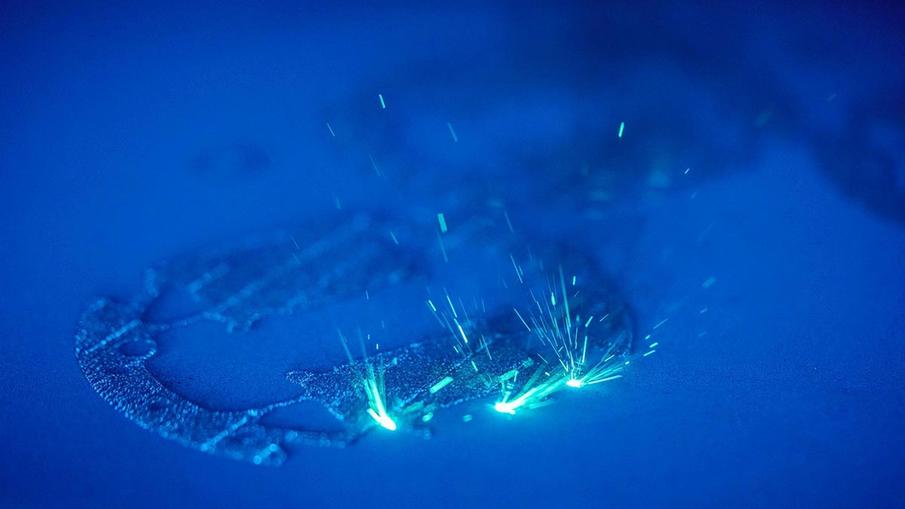
3D printing may seem like a completely new field, but various automotive manufacturers are very much in love with it. This is because 3D printing makes manufacturing easier and more efficient. The Volkswagen Group, for example, has been very active in 3D printed production. However, this has mostly been limited to the premium brands Bugatti and Porsche. In the future, however, Volkswagen has also stated that it will expand its 3D printing production. So what are the applications of 3D printing, which are used in cars?
There was a time when 3D printing seemed to revolutionise automotive manufacturing, and it must have been at least 10 years since the concept was created. But the most widespread use of 3D printing in automobiles today is not for production cars, but for the Formula 1 team, which produces fewer than 10,000 cars a year.
This means that it is produced in relatively small quantities. 3D printing has the advantage of being cheap, but the production speed is not yet suitable for mass production. Furthermore, in most cases, secondary processing is required, thus complicating the production process. Nevertheless, 3D printing is undoubtedly a very attractive production method. Bugatti is therefore using this method to manufacture various parts, including brake calipers, and Porsche says that the piston heads are designed to be 3D printed in order to increase production. BMW is also using 3D printing to produce some parts that have been discontinued.
However, it turns out that the Volkswagen Group has a considerable amount of experience in 3D printed production. Volkswagen claims to have been using 3D printing for 25 years. Of course it is difficult to tell with our naked eyes which ones are 3D printed. Volkswagen and many brands under the group are using 3D printing.
And now, Volkswagen will expand to a wider range. However, the production speed of 3D printing is still limited. A niche luxury brand like Bugatti or Porsche might be possible, but at least for a brand like VW, which produces millions of vehicles a year, it would be difficult to use this method.
For this reason, Volkswagen has introduced a new method. A new 3D printing method known in the industry as adhesive injection. Its most important feature is its increased productivity. The method used by Bugatti and Porsche is the laser irradiation method, in which a laser is used to selectively irradiate metal powder to shape it.
On the other hand, the spray adhesive powder forming process that Volkswagen has decided to opt for creates shapes by simultaneously spraying the material used as an adhesive and the powder, allowing complex colours to be achieved in one go. without the need for a separate colouring process. In addition, in this method, the strength can be adjusted by spraying the binder after completion. With recent improvements in the technology of the adhesive-bonded powder forming process, parts made from fairly strong materials can be produced without any problems.
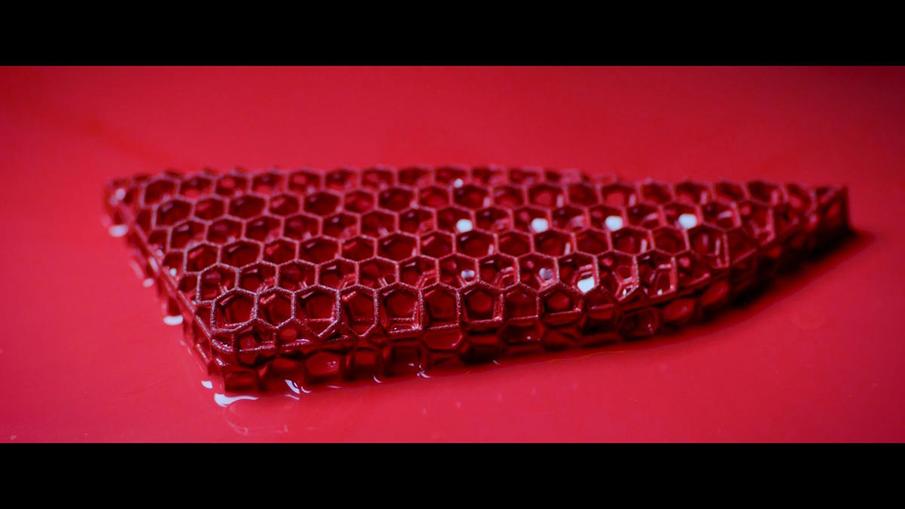
In addition, it is said that by improving the structure of the build chamber where the parts are manufactured, it is possible to ensure approximately twice the production volume compared to the existing production volume. The technology is being developed by HP and Siemens, with HP improving the structure of the printer and Siemens improving the software to provide 3D printing suitable for production lines that require high volumes, such as Volkswagen.
Volkswagen used this method to produce the A-pillar of the T-Roc Convertible, and the implications are considerable. For a convertible without a roof, the A-pillar serves as a safety support in the event of a rollover and can only be produced properly if it has sufficient strength. This is a testament to the maturity of 3D printing technology.
Volkswagen is not the first brand to produce its A-pillars in 3D printing - the Lexus LFA's A-pillar is also 3D printed and it is made from carbon fibre. In its own tests, Volkswagen says it has confirmed that it has gained sufficient strength. In addition, it is around 50% lighter than existing parts and cheaper to produce, so it could be an important strategic technology for the Volkswagen Group's drive to become carbon neutral by 2050. Volkswagen says it is ready to certify parts made using the technology.
The next step is to manufacture around 100,000 parts per year by 2025 using new 3D printing methods, if sufficient strength is ensured for the A-pillar of a convertible. Finally, almost all car manufacturers are currently looking for parts that are lighter and more robust. Volkswagen has found the answer in 3D printing. Perhaps they will find a new competitive edge in electric vehicles, which is a key focus for Volkswagen in the future.