Table of Contents:
- Introduction
- Design Principles for Plastic Parts
- Material Selection
- Injection Molding Process
- Prototyping and Testing for Plastic Parts
- Secondary Operations and Finishing Techniques
- Design for Manufacturing (DFM)
- Tooling and Production Costs
- Alternative Manufacturing Processes for Plastic Parts
- Future Developments and Applications of Plastic Part Design
- Conclusion
-
1.Introduction
Plastic part design is a crucial aspect of the manufacturing process that involves designing and engineering plastic components used in various applications. The design process involves the specification of a plastic material, determining the desired shape, size, and properties of the part, and ensuring that the part is functional and durable for its intended use.
The importance of plastic part design in manufacturing cannot be overemphasized, as plastic parts are used in many industries, including automotive, aerospace, construction, and medical. A well-designed plastic part can reduce manufacturing costs, eliminate waste, enhance product functionality and aesthetics, and ultimately increase the customer’s value.
The plastic manufacturing process involves turning raw plastic materials into useful products. It typically involves a series of stages, including materials selection, mold design, tooling, and post-processing operations such as finishing and secondary manufacturing processes. These processes require careful consideration of various factors, including the design of the part, the type of plastic used, and the specific manufacturing techniques deployed.
In the following sections, we will examine the principles and techniques of plastic part design, the factors to consider, the different types of materials, manufacturing processes, and finishing techniques. We will also discuss the importance of design for manufacturing (DFM) considerations and the impact of tooling and production costs. Finally, we will explore emerging trends in plastic part design and manufacturing, as well as future applications and potential innovations.
-
2.Design Principles for Plastic Parts
Designing plastic parts is a complex process that requires careful consideration of many factors to ensure that the part is functional, durable, and fit for its intended use. Below are some basic principles, factors to consider, and common design mistakes to avoid when designing plastic parts.
Basic Principles of Plastic Part Design:
- Design for the plastic manufacturing process: The design should take into account the plastic manufacturing process and be optimized for that process, whether it is injection molding, blow molding, or thermoforming.
- Material selection: Select a material that is fit for purpose, meets the required specifications, and is compatible with the manufacturing process.
- Part geometry: Ensure that the part’s geometry is designed for manufacturability, including features such as draft angles, fillets, and ribs, as appropriate for the manufacturing process.
- Wall thickness: Design parts with appropriate wall thicknesses to ensure strength and durability.
- Undercuts: Avoid designing features that create undercuts that cannot be released from the molds.
- Tolerances: Specify tolerances suitable for the manufacturing process and use them judiciously.
.
Factors to Consider When Designing Plastic Parts:
- The application and service conditions of the part, such as environmental conditions, load-bearing requirements, and temperature resistance.
- The intended volume of production, as high-volume production may require different design considerations.
- The level of precision and accuracy required in the part’s manufacturing and assembly.
- The material’s properties, including its strength, stiffness, and chemical resistance.
- The manufacturing process’s limitations, including the costs and cycle times of tooling, molding, and finishing operations.
- The intended users and their expectations around usability, functionality, and aesthetics.
.
Common Design Mistakes to Avoid:
- Designing parts without considering the manufacturing process and its limitations.
- Designing parts with excessive material or wall thickness, leading to high tooling, material, and production costs.
- Designing parts with features that cannot be released from molds, leading to defects and production delays.
- Failing to specify and adhere to tolerances required for the part’s function and use.
- Designing parts with sharp or hard edges that can impede assembly or cause injury.
- Failing to consider the assembly and interconnectivity of the parts within the product’s overall design.
In conclusion, plastic part design is a critical part of the manufacturing process, and careful consideration of several factors is essential to ensure a functional, durable, and cost-effective product. By following fundamental design principles, considering various factors, and avoiding common design mistakes, plastic part designers can optimize their designs for manufacturability, reduce production costs, and enhance the functionality and performance of the final product.
-
3.Material Selection
Selecting the right plastic material is fundamental to the success of any plastic part design. In this section, we will discuss the types of plastic materials used in part design, the selection criteria for different plastic materials, and the design considerations for different plastic types.
Types of Plastic Materials Used in Part Design
- Polyethylene (PE): A lightweight and flexible plastic used in a variety of applications, such as packaging films and bags, toys, and pipes.
- Polypropylene (PP): A rigid and durable plastic commonly used in automotive parts, packaging, and medical devices.
- Polystyrene (PS): A versatile and low-cost plastic used in packaging, toys, and disposable tableware.
- Acrylonitrile-butadiene-styrene (ABS): A tough and lightweight plastic used for automotive parts, toys, and electronic enclosures.
- Polyvinyl chloride (PVC): A flexible and durable plastic used in pipes, cables, and flooring.
- Polycarbonate (PC): A strong and impact-resistant plastic used in automotive parts, medical devices, and eyewear.
.
Selection Criteria for Different Plastic Materials:
- Environmental conditions: Select materials that are resistant to the intended environment, such as temperature and humidity.
- Service conditions: Consider the intended use of the part and select materials with appropriate strength, stiffness, and chemical resistance.
- Aesthetics: Choose materials that meet desired aesthetic and surface finish requirements.
- Processing capabilities: Select materials that are compatible with the processing techniques needed for manufacturing, such as injection molding or extrusion.
- Cost: Choose materials that balance cost and performance requirements.
.
Design Considerations for Different Plastic Types:
- Amorphous plastics, such as polycarbonate and acrylic, are transparent and brittle, and thus, require more design considerations to avoid cracking during manufacturing or use.
- Semi-crystalline plastics, such as polyethylene and polypropylene, are tougher and more resistant to deformation, but may require more complex tooling for injection molding.
- Elastomers, such as silicone and rubber, are flexible and stretchable, and require different design considerations, such as undercuts and draft angles, to facilitate release from molds.
In conclusion, selecting the appropriate plastic material is crucial to the success of any plastic part design. By considering factors such as environmental and service conditions, aesthetics, processing capabilities, and costs, designers can choose the right material for the part. Additionally, considering the unique design considerations required for different types of plastics, such as amorphous plastics or elastomers, can lead to more successful manufacturing outcomes.
-
4.Injection Molding Process
The injection molding process is one of the most popular plastic manufacturing processes used to create high-quality plastic parts. In this section, we will provide an overview of the injection molding process and highlight basic design considerations for injection molding. We will also discuss the tooling options available for injection molding and the cost implications for each.
An Overview of the Injection Molding Process:
- Material Selection: The selection of the material is an essential step in the injection molding process. The choice of material will depend on the intended use of the part, and several factors such as strength, flexibility, and durability.
- Mold Design: The mold design is based on the part’s size, shape, and requirements. The mold consists of two halves, a core, and a cavity. The core creates internal features, and the cavity forms external features.
- Injection Molding Machine: The machine melts the plastic pellets and injects them into the mold at high pressure.
- Cooling: After injection, the mold is cooled to a temperature that allows the plastic part to solidify and take shape.
- Ejection: Once the plastic part has cooled and solidified, the mold opens, and the part is ejected.
.
Basic Design Considerations for Injection Molding:
- Wall thickness: Design parts with uniform wall thickness to ensure proper cooling and minimize shrinkage.
- Ribs and Bosses: Design the part with proper ribs and bosses to support the structural integrity of the part within the mold cavity.
- Draft Angles: Design draft angles to facilitate the part’s release from the mold cavity without damaging the surface finish.
- Undercuts: Avoid designing parts with undercuts or use side actions in the tooling for part release.
- Parting Lines: Design the part with the proper parting line and ensure that it’s placed on flat or featureless surfaces.
.
Tooling Options and Cost Implications:
- Steel Tooling: Steel tools are durable and consistent, allowing for mass production. The cost of steel tooling is high but is the best choice for high-volume production.
- Aluminum Tooling: Aluminum tools are cheaper than steel tools and are easier to modify, but aluminum tools have a shorter lifespan than steel tools and are not suitable for high-volume production runs.
- Prototyping Tooling: Prototyping tooling uses less expensive materials like 3D printed molds, which can be made quickly and inexpensively. Prototyping tooling is suitable for small production runs.
In conclusion, the injection molding process is one of the most versatile plastic manufacturing processes used today. By considering basic design considerations such as wall thickness, draft angles, and undercuts, designers can ensure a successful injection molding process. Additionally, the choice of tooling options has different cost implications that impact the part’s design, production volume, and costs. Choosing the right tooling option ensures the success of the injection molding process and the quality of the final product.
-
5.Prototyping and Testing for Plastic Parts
Prototyping and testing are crucial components of plastic part design that help designers assess the functionality, durability, and manufacturability of a product. In this section, we will discuss why prototyping is essential, the different prototyping methods available, their benefits, and the testing protocols for plastic parts.
Importance of Prototyping in Plastic Part Design:
Prototyping is an essential step in plastic part design as it allows designers to validate their designs and identify potential issues before moving to mass production. Prototyping techniques allow the designer to test the product’s functionality, form-fit, and visual aesthetics, and helps in the making of any required modifications before full-scale production.
Different Prototyping Methods and Their Benefits:
- 3D Printing: 3D printing is an affordable and rapid prototyping method that produces parts directly from CAD models using a range of materials.
- CNC Machining: CNC machining is a process that involves cutting materials into shapes using precise computer-controlled machines. CNC machining produces parts from various materials such as plastics, metals, and ceramics.
- Vacuum Casting: Vacuum Casting is suitable for small production runs to produce parts for design evaluations, regulatory compliance, sales and marketing presentations and functional testing. It supports diverse materials, intricate geometries, and complex designs.
.
Testing Protocols for Plastic Parts:
- Mechanical Testing: Mechanical testing assess the resistance of the part to deformation, how long the part will last, and whether it is suitable for its intended use. Tests may include strength, shatter resistance, and compression testing.
- Chemical Testing: Chemical testing examines how the plastic part reacts to chemicals that it may come into contact with during its lifespan. The tests may include exposure to abrasive or corrosive agents, water, and other substances.
- Environmental Testing: Environmental testing assesses how the part will perform over time in a particular temperature, humidity, and weather conditions. Environmental tests may include thermal resistance, thermal cycling, and weathering tests.
In conclusion, prototyping and testing are critical components of plastic part design, which give an assurance to the designer about the functionality, manufacturability, and durability of the product. Using different prototyping methods such as 3D printing, CNC machining, and vacuum casting helps designers discover design flaws and make necessary modifications before proceeding to mass production. Furthermore, following testing protocols for mechanical, chemical and environment-ridden conditions helps to assess the product’s resistance and durability, ensuring the finished product offers high-quality service to its users.
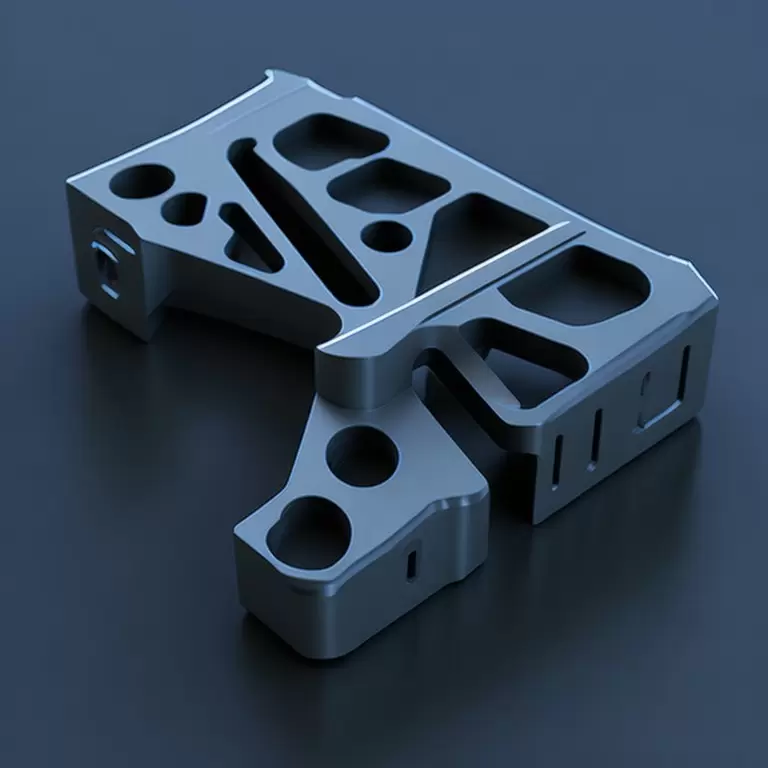
-
6.Secondary Operations and Finishing Techniques
Secondary operations and finishing techniques are critical in transforming plastic parts into finished products that meet functionality and aesthetic requirements. In this section, we will discuss common secondary operations for plastic parts and finishing techniques to enhance product functionality and appearance.
Common Secondary Operations for Plastic Parts:
- Machining: Machining refers to the process of cutting, drilling, and milling a plastic part to achieve a specific shape or dimension that cannot be achieved using the primary molding process.
- Welding: Welding refers to the process of joining two plastic parts using heat, pressure, or chemicals.
- Assembly: Assembly involves joining several plastic parts to create a complex finished product.
- Decorating: Decorating refers to adding graphics or colored finishes to the plastic part to enhance its aesthetic appeal.
.
Finishing Techniques to Enhance Product Functionality and Appearance:
- Painting: Painting involves adding a finish or color to a plastic part using either solvent or water-based paint to enhance its appearance.
- Coating: Coating involves adding a layer of protective material to the plastic part to enhance its resistance to chemicals and other external factors.
- Texturing: Texturing refers to creating a surface finish on the plastic part that provides a tactile feel or aesthetic look.
- Printing: Printing involves printing text or images onto the plastic part using various methods such as pad printing, hot stamping, or inkjet printing.
- Polishing: Polishing refers to the process of smoothening the surface of the plastic part to enhance its appearance and eliminate any sharp edges.
In conclusion, secondary operations and finishing techniques play a critical role in the production of high-quality plastic parts. The choice of secondary operations will depend on the product’s functionality and design requirements, while the finishing techniques should enhance the product’s appearance and tactile qualities. By considering the wide range of finishing techniques available and choosing the most suitable, designers can create a polished finished product that meets the functional and aesthetic needs of their customers.
-
7.Design for Manufacturing (DFM)
Design for Manufacturing (DFM) is a methodology that involves designing products that are optimized for the manufacturing process. In this section, we will discuss the importance of DFM in plastic part design, strategies for optimization, and balancing design with manufacturing requirements.
Importance of DFM in Plastic Part Design:
DFM is critical in plastic part design to ensure that designs can be manufactured cost-effectively, efficiently, and with minimal errors. By designing plastic parts with the manufacturing process in mind, companies can reduce production costs, minimize errors and waste, and shorten time-to-market.
Optimization Strategies for DFM:
- Material Selection: Opt for materials that are easy to process, have consistent properties, and offer good durability.
- Design for Uniform Wall Thickness: Consider designing for uniform wall thickness to ensure parts cool uniformly, minimizing distortion and shrinkage. Thick sections can also lead to higher gate pressure and increase the risk of stress and cracking.
- Maintaining Tolerance: Specify tolerance ranges in designs that adequately account for part variability allowed within the process.
- Incorporating Moldability: Consider incorporating features such as draft angles, radii, and fillets in the design, making the mold release and prevent cosmetic defects like flash or surface blemishes.
Balancing Design with Manufacturing Requirements:
Designers should ensure that their designs meet the manufacturing process’s requirements to achieve optimal manufacturing results. Designers should consider the production process steps closely at each stage of the development process, such as injection molding or extrusion.
It is essential to keep the design simplistic with fewer number of parts and avoiding the undercuts or complex features that demand complex tooling options.
Designers also need to consider the production volume, material selection, and part geometry when balancing design with manufacturing requirements. Balancing design decisions with manufacturing requirements ensures that the parts produced are of high quality, durable, and produced efficiently.
In conclusion, DFM is an essential part of plastic part design that can significantly reduce production costs, minimize errors, and shorten time-to-market. By optimizing the design for the manufacturing process, designers can ensure parts are produced efficiently with minimal waste or errors. Optimization strategies for achieving DFM include material selection, designing for uniform wall thickness, incorporating moldability, incorporating tolerance ranges, and balancing design with manufacturing requirements. Therefore, emphasizing DFM increases production efficiencies and positively affects the quality of the final product.
-
8.Tooling and Production Costs
Tooling and production costs are critical factors that determine a product’s overall cost and profitability. In this section, we will discuss an overview of tooling and production costs, factors that impact these costs, and strategies to minimize production costs.
Overview of Tooling and Production Costs:
Tooling is the process of creating molds, tools, and fixtures required to manufacture plastic parts. The cost for tooling depends on the complexity of the part’s design, the number of cavities in the mold, and the material used for the mold. Production costs, on the other hand, refer to the cost of materials, labor, machinery, and other overhead costs incurred during the production process.
Factors that Impact Costs:
Several factors impact tooling and production costs, including:
- Part complexity: Increased part complexity causes higher tooling costs and longer production times.
- Quality requirements: Higher quality requirements in the finished product may require tighter tolerances, more careful inspection, and additional production steps, leading to higher production costs.
- Production volume: The higher the production volume, the lower the production costs per unit since the overhead cost gets divided amongst the bulk productions.
- Material selection: The cost of manufacturing the part varies depending on the choice of material selected.
.
Strategies to Minimize Production Costs:
- Design for Manufacture: Utilize DFM methodology to minimize production costs by considering manufacturing requirements in the early stages of product design.
- Tooling options: In prototyping phases, designers can explore alternative options such as soft-sources like 3D printing before committing to higher-cost tooling.
- Part volume: By carefully forecasting demand for the product, it becomes clear to decide what production volumes require larger tools to get the job done in a timely and cost-efficient manner.
- Material selection: Choosing cost-effective materials with adequate mechanical, thermal, and other required properties to avoid excessive tool wear, tool failure, or unnecessary material expenses.
- Quality Control: Establishing robust quality control systems reduces warding-off of defects in finished products, which would otherwise raise the production cost by increasing scrap rates, re-work, returns or customer compensation.
In conclusion, tooling, and production costs are essential factors in determining a product’s overall cost and making it profitable. Understanding factors that impact the costs, strategies for minimizing production costs, and designing for manufacture can significantly contribute to reducing the costs. Therefore, careful planning and selection of appropriate manufacturing techniques and materials is vital in ensuring cost-efficient production of high-quality plastic parts.
-
9.Alternative Manufacturing Processes for Plastic Parts
There are various alternative manufacturing processes for plastic parts besides injection molding, such as vacuum forming, blow molding, casting, and additive manufacturing. In this section, we will discuss the overview of these alternative manufacturing processes, compare them, and their benefits and drawbacks.
- Vacuum Forming: Vacuum forming is a process that involves the formation of plastic sheets by heating a thermoplastic sheet until soft, then stretching it over a mold to create the desired part shape. The process is suitable for large, thin parts with low production volumes.
- Blow Molding: Blow molding is a process that involves forming a melted tube of plastic, called a parison, into a hollow mold. Compressed air is used to inflate the parison inside the mold until it takes on the desired shape. The process is suitable for plastic parts with irregular shapes and complicated geometries.
- Casting: Casting is a process that involves pouring a liquid thermoset or thermoplastic material into a mold and allowing it to harden. The process is suitable for parts with complex shapes and small production volumes.
- Additive Manufacturing: Additive Manufacturing or 3D Printing is a process that builds parts layer by layer using 3D printing techniques. It is suitable for producing parts with complex geometries and small production volumes.
.
Overview of Alternative Processes for Plastic Part Production:
Comparison of Different Manufacturing Processes:
- Production Volume: Injection molding is suitable for mass production, whereas vacuum forming, blow molding, and casting types are preferred for low to medium volumes.
- Tooling: Injection molding requires costly tooling expenses even for smaller order quantities. In contrast, vacuum forming, blow molding, casting, and additive manufacturing require lower tooling costs.
- Material Selection: Each process’s number of materials that can be used might differ from each other, for example, injection molding can use a broad range of materials such as thermoplastics and thermosets, whereas vacuum forming can only use thermoplastics.
- Part Complexity: Injection molding is well-suited for parts with higher levels of details and intricacies. In contrast, vacuum forming or casting may be better suited for parts with low to medium complexity.
.
Benefits and Drawbacks of Each Manufacturing Process:
- Injection Molding: Injection molding offers high production volumes, excellent part tolerance, and a range of materials to choose from. However, it is expensive, and the production of low-to-medium parts may not justify the upfront costs of tooling.
- Vacuum Forming: Vacuum forming offers low tooling costs, production of large parts, and excellent surface finish. However, part accuracy and tolerance may be inferior, and suitable solely for small to medium sizes.
- Blow Molding: Blow molding offers a high degree of production efficiency, strength and stiffness with the ability to produce complex geometries. However, limited material selection in comparison to injection molding, higher equipment cost, and thicker walls make it less precise than other plastic manufacturing methods.
- Casting: Casting offers the ability to produce complex shapes with high accuracy and texture finish. However, the process is more expensive, time-consuming, and labor-intensive than other processes.
- Additive Manufacturing: 3D printing offers almost unlimited geometries, lower tooling costs, and excellent customization option. However, comparatively slow production speed, comparatively wider range of post-processing, and limited material choice means specific material or precision requirements cannot be accommodated.
In conclusion, each plastic manufacturing process has unique benefits and drawbacks, depending upon production requirements, part complexity, production volume, and material choice. Choosing the right manufacturing process requires a deep understanding of the specific production parameters and the end use of the final plastic part. Understandably, the selection process can influence the success of the production process and the quality of the finished product.
-
10.Future Developments and Applications of Plastic Part Design
Plastic part design is a constantly evolving field, driven by developments in materials, innovative manufacturing technologies, and design optimizations. In this section, we will discuss emerging trends in plastic part design, potential applications for plastic parts in different industries, and predictions for future innovations and advancements.
Emerging Trends in Plastic Part Design:
- Sustainability and Circular Economy: Increasing emphasis on environmental sustainability has led to the growing need for using eco-friendly materials, reducing waste, and creating closed-loop systems.
- Smart Materials and IoT Integration: The integration of sensors and IoT technology in plastic parts will revolutionize product development and end-use applications, such as recycling tracking or asset tracking.
- Additive Manufacturing and 3D Printing: The growth of 3D printing opens up endless possibilities for complex designs with cleaner geometries and decreased material waste, resulting in economical and sustainable product designs.
- Bio-based Materials: The use of environmentally friendly, bio-based materials sourced from renewable resources like plants or marine life will be a significant trend toward achieving sustainable design practices.
.
Potential Applications for Plastic Parts in Different Industries:
- Automotive: Replacement of metal parts with lighter-weight, less expensive, and higher-performance plastic components.
- Healthcare: Development of new products with minimized risk of infection, personalization to individual medical needs, and time and cost efficiency.
- Electronics: 3D printing electronics, flexible and multi-material requirements, parts for devices in medical, aerospace, and other specialized industries.
- Construction: Innovative plastic parts like composite materials for functional integration (conduit’s protection, insulation, and structural reinforcement applications).
.
Predictions for Future Innovations and Advancements:
The future of plastic part design and manufacture appears very promising. The following are some anticipated innovations and advancements:
- Intelligent materials that are capable of diverse applications with improved performance and user-friendliness.
- Rapid, automated manufacturing technologies that lessen human intervention or labor need while maintaining quality production, reducing the costs of production.
- Further adoption of sustainable and circular economy methodologies and multi-purpose product designs aiming to lessen ecological degradation and environmental impact.
- Advanced additive manufacturing techniques like robotic 3D printing for complex or miniaturized small-quantity production, as well as precise and consistent results in large-scale production.
In conclusion, the future of plastic part design will take into account the environmental, economic and societal needs in product development. Creative designers will shift toward using sustainable and eco-friendly materials and innovative manufacturing technologies to create products that are lightweight, less expensive, higher-performance, with integration of smart technologies. Therefore, the application of creative solutions in plastics manufacturing offers endless opportunities capable of addressing current and future societal requirements.
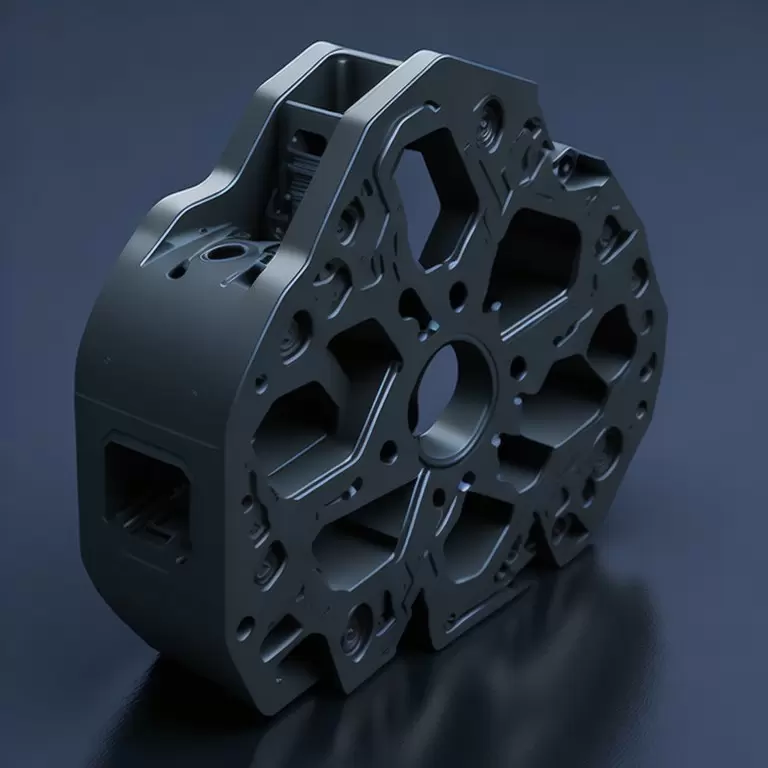
-
11.Conclusion
Plastic part design and manufacturing have come a long way, from simple parts to increasingly complex parts, using more sophisticated tools and machines. Designers face significant challenges in creating sustainable, affordable, high-performance plastic parts while considering changes in industry demands and technological advancements. Key concepts such as design for manufacturing, material selection, tooling and production costs, alternative manufacturing processes have been discussed, emphasizing the importance of applying them in creating efficient and effective plastic parts.
Collaboration between designers and manufacturers is essential in ensuring that the product is not only designed for function, but also considers efficient materials, manufacturing processes, and production costs. Thus, designers must work closely with manufacturing experts to develop and produce products that are of high-quality, cost-effective, and eco-friendly.
In the future, there will undoubtedly be more developments in plastic part design and manufacturing. Specifically, emerging trends such as the integration of IoT technology and 3D printing and the adoption of sustainable materials demonstrate the promise of further innovation in this sector. The future will be shaped by the ability of producers to adapt and apply innovative plastic parts designs to meet evolving industry demands and market trends.
In conclusion, plastic part design and manufacturing will undoubtedly continue to play a significant role in the development and creation of sustainable and innovative product designs. By continuing to collaborate and invest in advanced technologies and methodologies, designers and manufacturers look forward to reaching their goals while overcoming the challenges ahead.