Injection moulding is a widely used manufacturing process that has revolutionized the production of plastic products. It is a cost-effective and versatile method that enables the creation of complex shapes and structures with great accuracy and consistency. In this article, we will explore the injection moulding process in detail, its advantages and disadvantages, and its wide range of applications.
What is Injection Moulding?
Injection moulding is a manufacturing process that involves the use of a mould or tool, made from metal, which has a cavity in the shape of the desired product. The mould is then placed into an injection moulding machine, which is a complex piece of equipment that is capable of melting plastic pellets and injecting them into the mould.
The plastic pellets are fed into a heated barrel, where they are melted and mixed to form a homogenous material. Once the material reaches the desired temperature and consistency, it is injected into the mould at a high pressure. The plastic is then cooled and solidified inside the mould, and the finished product is ejected.
Advantages of Injection Moulding
One of the key advantages of injection moulding is its ability to produce large quantities of products in a short amount of time. The process is highly automated, and the cycle times can be as short as a few seconds, depending on the size and complexity of the product.
Injection moulding is also a cost-effective method of manufacturing. The initial setup cost for the production of a mould is relatively high, but the cost per unit decreases as the volume of production increases. This makes injection moulding an ideal solution for high-volume production runs, as the cost per unit can be significantly reduced.
Another advantage of injection moulding is its ability to create complex shapes and structures with great accuracy and consistency. This is achieved through the use of precision tools and machines, which ensure that each part is identical to the last. Injection moulding also allows for the use of a wide range of materials, including thermoplastics, thermosetting plastics, and elastomers.
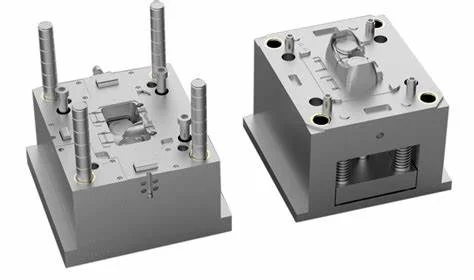
Disadvantages of Injection Moulding
Despite its many advantages, injection moulding has some limitations. One of the main limitations is the high initial setup cost for the production of a mould. This cost can be prohibitive for small-scale production runs or for products that require frequent design changes.
Another limitation is the size and complexity of the products that can be produced. Although injection moulding can produce large, complex structures, there are limits to the size and thickness of the parts that can be produced. Additionally, the process may not be suitable for products that require a high level of surface finish, as the moulding process can leave a textured or rough surface.
Applications of Injection Moulding
Injection moulding is used in a wide range of industries, including automotive, medical, consumer goods, and electronics. It is particularly well-suited to the production of high-volume products, such as plastic toys, packaging materials, and components for electronic devices.
In the automotive industry, injection moulding is used to produce a range of components, including dashboard panels, interior trim, and exterior body parts. The process is also used in the production of medical devices, such as syringes, vials, and other plastic components.
One of the key benefits of injection moulding is its ability to produce complex shapes and structures with great accuracy and consistency. This makes it a popular choice for the production of consumer goods, such as kitchen appliances, electronic devices, and household items.