Plastic injection mold machines are widely used in the manufacturing industry for producing plastic parts and products. These machines use a process called injection molding to melt and inject plastic materials into molds, which are then cooled and solidified into the desired shape. In this article, we will discuss the types of plastic injection mold machines, their advantages, and some maintenance tips to keep them in optimal condition.
- Types of Plastic Injection Mold Machines
- Advantages of Plastic Injection Mold Machines
- Maintenance Tips for Plastic Injection Mold Machines
- Common Issues and Troubleshooting Techniques
- Conclusion
Types of Plastic Injection Mold Machines
There are several types of plastic injection mold machines, including:
• Hydraulic Injection Molding Machines: These machines use hydraulic power to operate the injection process. They are known for their high production output and ability to handle large molds.
• Electric Injection Molding Machines: These machines use electric power to operate the injection process. They are known for their precision, energy efficiency, and low noise levels.
• Hybrid Injection Molding Machines: These machines combine hydraulic and electric power to operate the injection process. They offer the benefits of both hydraulic and electric machines, including high production output and energy efficiency.
Advantages of Plastic Injection Mold Machines
Plastic injection mold machines offer several advantages, including:
• High Production Output: Injection molding is a fast and efficient process that allows for high production output.
• Precision and Accuracy: Injection molding allows for precise and accurate production of plastic parts and products.
• Versatility: Injection molding can produce a wide range of plastic parts and products of various shapes, sizes, and complexity.
• Cost-Effective: Injection molding can be cost-effective for large-scale production runs due to the high production output and efficiency of the process.
Maintenance Tips for Plastic Injection Mold Machines
Proper maintenance is crucial for keeping plastic injection mold machines in optimal condition. Here are some maintenance tips to consider:
• Regular Cleaning: Regular cleaning of the machine's components, including the hopper, barrel, and mold, can help prevent contamination and prolong the machine's lifespan.
• Lubrication: Proper lubrication of the machine's moving parts can help reduce friction and wear, and improve the machine's performance.
• Inspection: Regular inspection of the machine's components can help detect any issues or wear and tear, and prevent them from turning into major problems.
• Calibration: Regular calibration of the machine's controls and sensors can help ensure accurate and precise production.
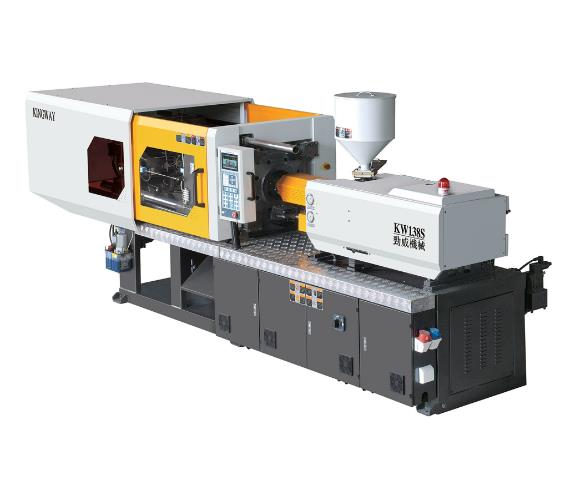
Common Issues and Troubleshooting Techniques
Despite proper maintenance, plastic injection mold machines can still experience issues that require troubleshooting. Here are some common issues and troubleshooting techniques:
• Warpage: Warpage can occur when the plastic material cools unevenly or too quickly. Troubleshooting techniques include adjusting the cooling time or temperature, and adjusting the mold design.
• Flash: Flash is excess plastic material that forms around the edges of the mold. Troubleshooting techniques include adjusting the clamping force, reducing the injection speed, or adjusting the mold design.
• Sink Marks: Sink marks are depressions that form on the surface of the plastic part due to uneven cooling. Troubleshooting techniques include adjusting the cooling time or temperature, and adjusting the mold design.
Conclusion
Plastic injection mold machines are a vital tool in the manufacturing industry for producing plastic parts and products. They offer several advantages, including high production output, precision, versatility, and cost-effectiveness. Proper maintenance, including regular cleaning, lubrication, inspection, and calibration, is crucial for keeping these machines in optimal condition. Despite proper maintenance, these machines can still experience issues that require troubleshooting. With the proper maintenance and troubleshooting techniques, plastic injection mold machines can provide long-lasting performance and reliability.
Overall, plastic injection mold machines are a valuable investment for companies looking to produce plastic parts and products efficiently and cost-effectively. By understanding the different types of machines, their advantages, and proper maintenance techniques, companies can ensure their machines are running at optimal performance and avoid costly downtime due to maintenance issues or production defects.
When selecting a plastic injection mold machine, it is important to consider the specific needs and requirements of the production process. Factors such as the size and complexity of the parts or products, production output, and budget should be taken into account to determine the most suitable machine for the job.
In addition, companies should also consider the training and expertise of their operators, as proper operation and maintenance of these machines are crucial for their longevity and performance. Regular training and education can help ensure that operators are up-to-date on the latest techniques and best practices for operating and maintaining these machines.
In conclusion, plastic injection mold machines are a valuable tool for companies in the manufacturing industry, offering high production output, precision, versatility, and cost-effectiveness. Proper maintenance and troubleshooting techniques are crucial for ensuring optimal performance and reliability, and selecting the right machine for the job is important for achieving the desired production output and quality. With the right investment, training, and maintenance, plastic injection mold machines can provide long-lasting performance and contribute to the success of the manufacturing process.