Table of Contents:
- Introduction to Aluminium Extrusion
- The Aluminium Extrusion Process
- Advanced Techniques for Aluminium Extrusion
- Aluminium Extrusion Applications
- Benefits and Advantages of Aluminium Extrusion
- Safety Considerations for Aluminium Extrusion
- Future of Aluminium Extrusion
- Conclusion and Resources
-
1. Introduction to Aluminium Extrusion
Aluminium extrusion is the process of shaping aluminum into a specific profile, using a die and a press. The result is a single, continuous piece with an intricate cross-section. In this guide, we will explore the various techniques, applications, and benefits of aluminum extrusion.
A. Overview of Aluminium Extrusion
Aluminium extrusion offers many benefits over other manufacturing processes, including the ability to create complex shapes and designs with a high level of accuracy and consistency. The process provides a cost-effective, sustainable solution for the production of high-quality aluminum products.
B. Benefits of Aluminium Extrusion
Some of the benefits of aluminium extrusion include its flexibility, precision, and durability. Extruded aluminum is lightweight, yet strong, and can be finished to meet a wide range of design requirements. It is also a cost-effective and sustainable alternative to other metal fabrication processes.
C. Types of Aluminium Extrusions
There are several types of aluminum extrusions, each with its own application and benefits. These include standard profiles, custom profiles, and specialty profiles. Standard profiles are mass-produced and available in a variety of shapes and sizes. Custom profiles are designed for specific applications and can be made to order. Specialty profiles are designed for specific industries and applications, such as aerospace or automotive.
-
2. The Aluminium Extrusion Process
In order to create a high-quality aluminum extrusion, several steps are involved in the extrusion process.
A. Design Process Overview
The design process begins with a digital model of the aluminum extrusion. The model is used to create a die, which is the tool used to shape the aluminum into the desired profile.
B. Extrusion Die Selection and Design
The die is selected based on the desired profile and must be designed to withstand the forces of the extrusion process. The die is then machined to create the desired shape and size.
C. Billet Preparation and Heating
Aluminum billets are heated to a specific temperature to ensure they are pliable enough to be shaped by the die. This temperature is critical and must be precisely controlled throughout the extrusion process.
D. Extrusion Process
The billet is loaded into the press, where it is compressed and forced through the die. The extrusion emerges from the other side of the die as a continuous piece of aluminum with the desired profile.
E. Finishing and Fabrication
The finished extrusion may require further processing, such as cutting, drilling, or bending. It will also be finished with surface treatments, such as anodizing or painting, to meet the required specifications.
-
3. Advanced Techniques for Aluminium Extrusion
Once you have mastered the basics, there are a range of advanced techniques that can take your aluminum extrusion to the next level.
A. Cooling Techniques
Cooling techniques are used to control the temperature of the extruded aluminum and minimize distortion or warping. These include water quenching, air cooling, or a combination of both.
B. Pre- and Post-Extrusion Processing
Pre- and post-extrusion processing can include any additional processing steps required to meet the desired specifications. This can include annealing, stress relieving, or straightening.
C. Secondary Operations
Secondary operations may be required to create the final product, such as cutting, drilling, or bending. These processes must be done with care to ensure that the desired tolerances are met.
D. Specialty Extrusion Techniques
Specialty extrusion techniques may be required to create unique profiles or to meet specific industry requirements. Examples include hydroforming, heat sinking, or multi-cavity extrusion.
E. Trouble Shooting Tips
Despite careful design and planning, extrusion problems can still occur. Understanding common problems such as die lines, porosity, and oxidation can help troubleshoot issues quickly and efficiently.
-
4. Aluminium Extrusion Applications
Aluminium extrusion is used in a variety of industries and applications. Some of these include:
A. Architectural Applications
Aluminium extrusions are commonly used in architectural applications, such as windows, doors, and curtain walls. The ability to create unique, complex shapes makes aluminum extrusions a popular choice for designers and architects.
B. Automotive and Transportation Applications
Aluminium extrusions are used extensively in automotive and transportation applications, such as aircraft and automotive frames. The strength and durability of aluminum make it a popular choice for these high-stress applications.
C. Industrial Applications
Aluminium extrusions are used in a variety of industrial applications, such as heat sinks, frames, and conveyor systems. The strength and durability of aluminum make it a popular choice for demanding industrial applications.
D. Electrical and Electronic Applications
The electrical and electronic industries use aluminium extrusions for the creation of enclosures, heat sinks, and other components. The ability to create precise shapes and sizes makes aluminum extrusions ideal for these applications.
E. Consumer Goods Applications
Aluminium extrusions are used in a variety of consumer goods, such as furniture, bicycles, and sporting goods. The lightweight and customizable nature of aluminum extrusions make them an attractive option for these industries.
-
5. Benefits and Advantages of Aluminium Extrusion
There are many benefits and advantages of using aluminum extrusion in your manufacturing process.
A. Material Properties
Aluminum extrusions offer a range of beneficial material properties, such as strength, durability, and corrosion resistance. The lightweight nature of aluminum also makes it a popular choice for applications where weight is a concern.
B. Design Flexibility
Aluminum extrusions offer a high degree of design flexibility, enabling you to create custom profiles that meet your exact specifications. This flexibility allows for creative and innovative designs that traditional metal fabrication processes may not be able to achieve.
C. Strength and Durability
Aluminum extrusions are incredibly strong and durable, enabling them to withstand high-stress applications. Because of their strength and durability, aluminum extrusions can reduce the overall weight of a product without compromising its functionality or strength.
D. Cost-Effectiveness
Aluminum extrusion is a cost-effective alternative to other metal fabrication processes due to the reduced need for machining and the ability to mass-produce identical profiles. This process can save you time and money in the long run.
E. Sustainability
Aluminum extrusion is a sustainable manufacturing process, as it produces minimal waste and can be recycled indefinitely. This process supports environmentally conscious manufacturing processes and can reduce your carbon footprint.
-
6. Safety Considerations for Aluminium Extrusion
As with any manufacturing process, safety is of the utmost importance when working with aluminum extrusion.
A. Personal Protective Equipment (PPE)
The use of personal protective equipment, such as safety glasses, gloves, and ear protection, is essential to prevent accidents and protect against hazards during the extrusion process.
B. Safe Handling Procedures
Proper handling procedures for billets and extrusions are critical to prevent accidents, such as pinch points or crushing. These procedures should be implemented by all personnel involved in the extrusion process.
C. Fire Suppression and Prevention
There is a risk of fire during the extrusion process. Fire suppression and prevention measures, such as proper dust and chip removal, proper coolant selection and disposal, and regular machine maintenance, must be put in place to minimize this risk.
D. Maintenance and Inspection
Regular maintenance and inspection of the extrusion press and dies are essential to ensure safe and efficient operation. Regular inspection can help identify and address potential safety hazards before they become a bigger issue.
-
7. Future of Aluminium Extrusion
The future of aluminium extrusion is bright, with potential for new developments and advanced technologies to revolutionize the industry.
A. Emerging Technologies
Emerging technologies, such as 3D printing and additive manufacturing, are already being incorporated into aluminium extrusion processes. Advanced automation and artificial intelligence technologies can further improve efficiency, quality, and precision in the extrusion process.
B. Innovations and Trends
New innovations and trends in extrusion technology are likely to emerge, including new alloy compositions, surface treatments, and finishing techniques.
C. Forecast for the Aluminium Extrusion Industry
The aluminium extrusion industry is poised for continued growth in the coming years, driven by increasing demand for lightweight, durable materials in a variety of industries.
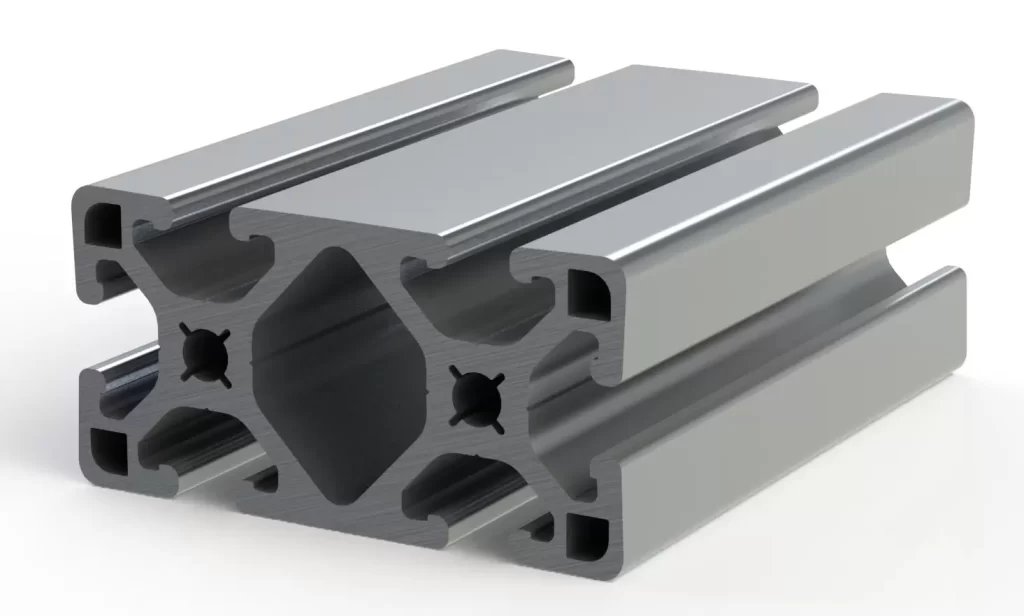
-
8. Conclusion and Resources
Aluminium extrusion is a versatile, flexible, and cost-effective alternative to other metal fabrication processes. By understanding the extrusion process, mastering advanced extrusion techniques, and following safety procedures, designers and manufacturers can create precise, high-quality parts and products. Additional resources for learning about aluminium extrusion include online tutorials, forums, industry publications, and conferences.