Table of Contents:
- Introduction to Molding Products
- Types of Molding Products
- Materials Used in Molding Products
- Molding Processes
- Applications of Molding Products
- Best Practices for Creating Molding Products
- Trends and Innovations in Molding Products
- Challenges and Solutions in Molding Product Manufacturing
- Conclusion and Future Outlook
-
1. Introduction to Molding Products
A. What are Molding Products?
Molding products are industrial products and parts manufactured using specialized molding manufacturing processes such as injection molding, blow molding, thermoforming, rotational molding, and extrusion molding.
B. Importance of Molding Products
Molding products are essential in modern manufacturing due to their ability to create identical items accurately and precisely. Molding products are versatile, cost-effective, and can be made with a wide range of materials.
C. Benefits of Working with Molding Products
Working with molding products offers many benefits, including faster turnaround times, reduced production downtime, and lower costs, especially for high-volume production runs.
-
2. Types of Molding Products
A. Injection Molding Products
Injection molding is a popular molding process, used widely in the creation of complex parts such as automotive parts, medical devices, and electronic components.
B. Blow Molding Products
Blow molding is a process that can create large, hollow items such as containers or bottles for the packaging industry.
C. Thermoforming Products
Thermoforming is a method of creating molded products that involve heating and reshaping sheet plastic into specific forms, such as trays or blister packs.
D. Rotational Molding Products
Rotational molding is a process that involves heating and rotating hollow plastic molds to create seamless products such as fuel tanks or playground equipment.
E. Extrusion Molding Products
Extrusion molding is the process of creating continuous, uniform products such as tubing or pipes.
-
3. Materials Used in Molding Products
A. Thermoplastics
Thermoplastics are versatile materials that can be melted and remolded many times. Common thermoplastics include polyethylene, polypropylene, and polystyrene.
B. Thermosetting Plastics
Thermosetting plastics can only be molded once and will solidify permanently after molding. Examples of thermosetting plastics include phenolics, melamine, and urea.
C. Elastomers
Elastomers are flexible, stretchy materials used for molding products that need to be bendable or have shock-absorbing properties. Examples of elastomers are rubber and silicone.
D. Metals
Metals such as aluminum and steel can also be molded using specialized techniques such as casting and forging.
-
4. Molding Processes
A. Mold Design
The quality of the final product is largely influenced by the mold design. The mold design takes into account factors such as injection pressure, cooling speed, and temperature.
B. Mold Fabrication
Mold fabrication involves making molds made of metal or non-metallic materials, depending on cycle times, structural demands, and material limitations.
C. Injection Molding Process
The injection molding process begins by heating and melting molding materials, which are then injected into the mold cavity. The material cools, and the mold opens, releasing the finished product.
D. Post-Molding Operations
Post-molding operations, such as trimming or polishing, are used to remove excess material and improve the final product’s surface finish.
-
5. Applications of Molding Products
A. Automotive Industry
Molding products are widely used in the automotive industry for parts such as dashboards, bumpers, and electrical components.
B. Medical Industry
Precision molding products engineering is essential for medical devices, implants, and tools requiring high dimensional accuracy and strict regulatory compliance.
C. Packaging Industry
Molding products are common in the packaging industry for creating products such as bottles, jars, and containers.
D. Consumer Goods Industry
Molding products are popular in the consumer goods industry for creating everyday items such as toys, kitchenware, and electrical appliances.
E. Electronics Industry
Molding products are widely used in the electronics industry for creating parts such as television casings, keyboards, and computer hardware.
-
6. Best Practices for Creating Molding Products
A. Material Selection
Choosing the right material for the final product involves considerations such as durability, chemical resistance, or environmental factors.
B. Mold Design and Fabrication Quality
Mold quality plays a critical role in the final product. High-quality molds made of high-quality materials improve overall output and reduce the need for maintenance and repairs.
C. Quality Control and Testing
Quality control and testing ensure products meet the desired specifications, quality standards, and regulations.
D. Communication and Transparency
Effective communication between manufacturers leads to a collaborative and productive working relationship.
-
7. Trends and Innovations in Molding Product Manufacturing
A. Sustainable Materials and Processes
Materials and production processes focused on sustainability, including bioplastics or recycled plastics, are becoming popular in molding product manufacturing.
B. Industry 4.0 Technologies
Integration of advanced technologies like Internet of Things (IoT) and artificial intelligence (AI) into molding product manufacturing improves efficiency, accuracy, and productivity.
C. Advanced Mold Design and Fabrication Techniques
Advanced mold design and fabrication techniques, including additive manufacturing and nanotechnology, have opened new frontiers for the industry.
If you need about Molding Product information,You can click on the V1 Prototype website to find it.
-
8. Challenges and Solutions in Molding Product Manufacturing
A. Cost and Time Constraints
Scaling up the production of molding products can pose challenges related to cost and time constraints. Employing smart manufacturing and 3D printing can help to address these challenges and reduce manufacturing costs.
B. Material Selection and Performance
Molding products require high-performing materials that meet specific performance and quality standards, especially in applications involving high temperatures, pressure, or other environmental factors. Employing advanced materials and coatings can help address some of these challenges.
C. Design and Quality Control
Producing high-quality products with complex shapes and structures can pose challenges due to factors such as part geometry, mold design, and process variability. Employing statistical process control (SPC) and finite element analysis (FEA) can help improve the design and quality control processes.
D. Technological Adaptation
As molding product manufacturing continually evolves, manufacturers must adapt to the latest technological advances to remain competitive and meet changing market demands. Continuous training and investment in cutting-edge technologies can help manufacturers stay ahead of the curve.
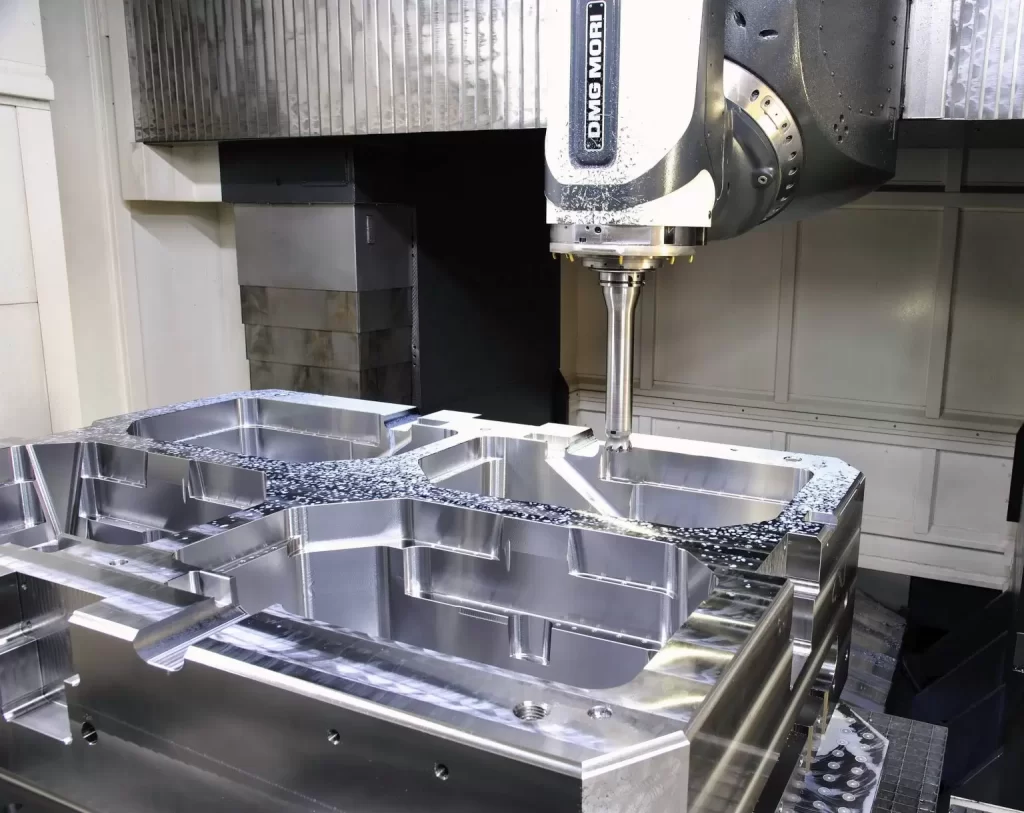
-
9. Conclusion and Future Outlook
A. Summary of Key Points
Molding product manufacturing enables companies to produce high-quality products with complex shapes and structures quickly and cost-effectively. Advances in materials, machinery, and technology are continuously driving the industry forward.
B. Future of Molding Product Manufacturing
The future of molding product manufacturing is bound to see an increase in automation, integration of Industry 4.0 technologies, and sustainable practices like the use of bio-degradable materials.
C. Resources for Further Learning
Academic research, technical publications, and industry associations provide great resources for learning about the latest developments in molding product manufacturing and best practices. Keeping up with current trends and advancements can help companies stay competitive and produce high-quality products that meet changing market demands.
In conclusion, molding product manufacturing plays a crucial role in modern manufacturing, producing high-quality products quickly and cost-effectively. The industry is likely to see advancements in automation, advanced materials, and integration of Industry 4.0 technologies, making it more productive and sustainable. The challenges of material selection and performance, design and quality control, and technological adaptation need to be addressed through continuous investments in cutting-edge technology and training to maintain a competitive edge.