Development Prospect of Die Casting
Die casting is a widely used manufacturing process for producing metal components with high precision and complex geometries. As the demand for lightweight and durable metal parts continues to grow in industries such as automotive, aerospace, electronics, and consumer goods, die casting holds a promising development prospect. Advancements in die casting technology, including improved materials, process efficiency, and automation, are driving its adoption in various applications. Additionally, die casting's ability to achieve high production rates and cost-effectiveness positions it as a favored method for mass production of metal components.
Quality in Die Casting
The quality of die-cast parts is essential to meet industry standards and ensure the reliability and performance of the final products. Several factors contribute to the quality of die-cast parts:
- Material Quality: The choice of metal alloy plays a critical role in the final part's properties. High-quality materials with the right composition ensure the desired mechanical properties and surface finish.
- Die Design and Maintenance: Well-designed and maintained dies help in producing parts with consistent dimensions and reduced defects.
- Process Control: Tight process control, including monitoring of temperature, pressure, and injection speed, is vital for achieving uniform and defect-free castings.
- Porosity and Shrinkage: Proper gating and venting designs are necessary to minimize porosity and shrinkage defects in the castings.
- Surface Finish: Surface finish can impact the part's appearance and functionality. Proper die polishing and surface treatment contribute to achieving the desired finish.
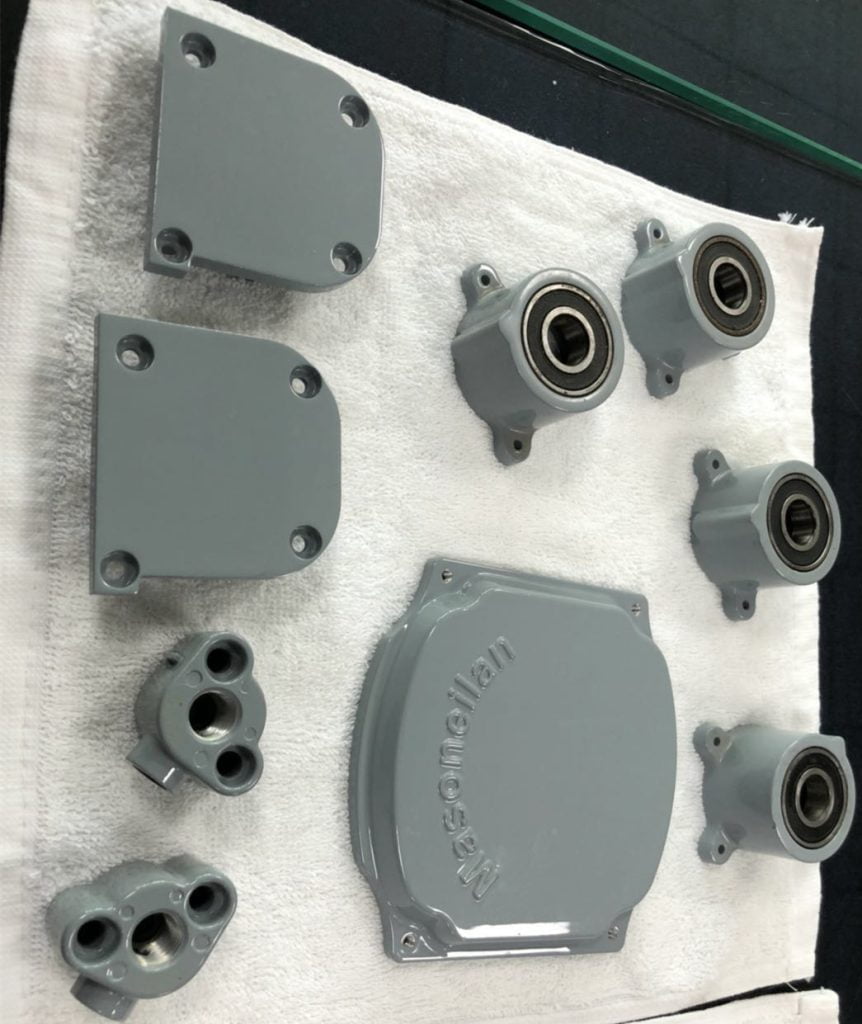
Output and Efficiency
The output of die casting largely depends on several factors, including the complexity of the part, the size of the die casting machine, and the cycle time. Die casting machines come in various sizes, ranging from small to large, enabling the production of parts of different sizes and complexities. High-pressure die casting machines are known for their rapid cycle times, contributing to higher output rates and increased efficiency in mass production.
Common Problems in Die Casting
While die casting offers numerous advantages, it is not without its challenges. Some common problems encountered in die casting include:
- Porosity: Gas trapped in the molten metal can cause porosity in the final part, leading to reduced mechanical strength.
- Cold Shut: Cold shut occurs when two portions of molten metal fail to fuse completely during the casting process, resulting in incomplete filling of the mold.
- Flash: Excess material escaping from the die-casting mold can cause flash, which needs to be trimmed after the casting process.
- Die Wear: Repeated use of dies can lead to wear and erosion, affecting the dimensional accuracy and surface finish of the parts.
- Soldering: Soldering occurs when molten metal adheres to the die surface, leading to defects in subsequent castings.
Conclusion
Die casting continues to be a valuable manufacturing process with a promising development prospect due to its ability to produce high-quality metal components efficiently. Advancements in die casting technology, coupled with process optimization and enhanced material properties, are driving its adoption across various industries. While challenges such as porosity, flash, and die wear exist, ongoing research and continuous improvement in die casting techniques are addressing these issues and further enhancing the process's capabilities. With a focus on quality, efficiency, and innovation, die casting remains a preferred method for producing precise and complex metal parts in large quantities.
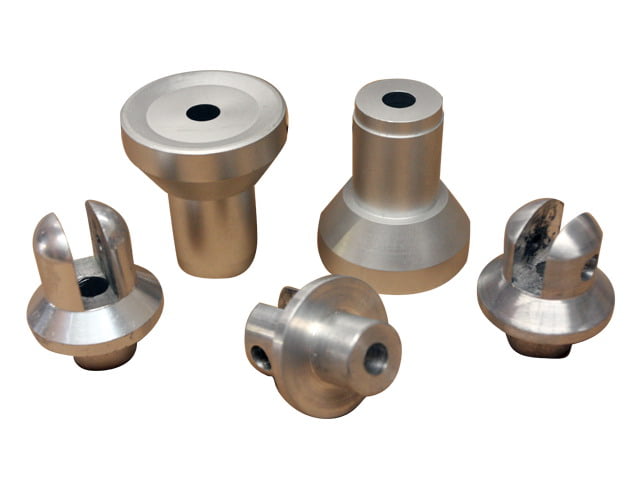
Q&A
Part of the die casting is not formed and the cavity is not sufficient
Causes: 1. The die casting mold temperature is too low; 2. Low temperature of liquid metal; 3, the press pressure is too small; 4. Insufficient liquid metal; The injection velocity is too high; 5, air can not be discharged.
Adjustment method: 1-2, raise die casting mold, metal liquid temperature; 3. Replace the high pressure die casting machine; 4. Add enough liquid metal to reduce the injection speed and increase the thickness of the feed port.