Table of Contents:
- Introduction to 3D Printed Injection Molds
- Basic Design Principles for 3D Printed Injection Molds
- Process of 3D Printed Injection Molds
- Applications of 3D Printed Injection Molds
- Quality Control and Inspection in 3D Printed Injection Molds
- Advancements and Future Trends in 3D Printed Injection Molds
- Comparison between 3D Printed Injection Molds and Other Mold Making Methods
- Conclusion
-
1. Introduction to 3D Printed Injection Molds:
The manufacturing industry is undergoing a paradigm shift with the integration of 3D printing with traditional manufacturing practices. The 3D printing technology is being used for rapid prototyping and small-batch production. Among the varied applications of 3D printing technology, the use of 3D printed injection molds is garnering increasing interest. This article aims to provide an in-depth guide on 3D printed injection molds, highlighting the advantages, limitations, design principles, processes, applications, quality control measures, advancements, and comparisons with other mold making methods.
Advantages and Limitations of 3D Printed Injection Molds:
The major advantage of 3D printed injection molds is the cost-effectiveness associated with producing molds with high accuracy and detail in a shorter span of time than traditional machining. With a 3D printer, molds are customized and prepared within hours, not days. This allows unlimited design freedom and helps to minimize the costs associated with traditional mold making methods.
However, there are some limitations. One of the major limitations of 3D printed injection molds is their rigidity and inability to handle high temperatures or pressures. Additionally, 3D printed injection molds are limited to fewer materials than traditional injection molding processes.
-
2. Basic Design Principles for 3D Printed Injection Molds:
Choosing the Right Material:
Selecting the appropriate 3D printing material for injection molding is a crucial task. The material used must have the required properties, including thermal resistance, mechanical strength, and durability, to meet the demands of the injection molding process.
Considerations for Designing the Mold:
Designing the 3D printed injection mold includes considering the right relief angles, engineering avoid undercuts, and ensuring proper spacing of the mold parting surface. The injection mold design should also accommodate sufficient channels and gates to channel the molten material.
Preparing the 3D Printer:
For 3D printed injection mold making, an industrial-grade 3D printer is recommended. The printer must have a larger build volume for larger molds, as well as high precision and accuracy.
-
3. Process of 3D Printed Injection Molds:
Creating the Mold Design:
The first step to make a 3D printed injection mold is to design the mold in a CAD software. The design should consider elements such as gates, runners, and sprues, as well as the injection molding machine’s size.
3D Printing the Mold:
The second step in manufacturing 3D printed injection molds is to use the CAD design to print the mold. Depending on the size and complexity of the design, the printing can take several hours or days.
Finishing and Post-Processing the Mold:
Once the 3D printed injection mold is complete, it’s time to clean and finish it, typically through machining or polishing. The final product is a high-quality, customized injection mold that is ready to be loaded with resin and used.
-
4. Applications of 3D Printed Injection Molds:
Small-batch Production:
3D printed injection molds are widely used in small-scale manufacturing, especially in the production of plastic parts that require small production runs.
3D printed injection molds can produce prototypes of parts in a matter of hours instead of days or weeks, enabling manufacturers to save valuable time and money during the research and development stage.
Custom Mold Design:
The ability to easily modify designs of 3D printed injection molds provides manufacturers with unlimited possibilities for customizing molds to match their specific requirements.
-
5.Quality Control and Inspection in 3D Printed Injection Molds:
Key Metrics in 3D Printed Injection Molds Quality Control:
To check the quality of 3D printed injection molds, critical metrics to monitor include dimensional accuracy, surface finish, and the ability of the mold to withstand injection molding.
QC Techniques and Approaches:
Non-destructive testing, visual inspection, microscopic examination, and mechanical testing methods are used to check mold quality.
Safety and Regulatory Challenges and Considerations:
3D printed injection molds require the operator to wear protective gear, as the materials and tools can be hazardous, and they carry specific regulations/guidelines of individual countries.
-
6. Advancements and Future Trends in 3D Printed Injection Molds:
Advancements in 3D Printed Injection Mold Technology:
With the development of more advanced 3D printing technologies, including new materials, higher precision, and faster print speeds, the use of 3D printed injection molds is set to revolutionize the manufacturing industry.
Increasing Sustainability:
Sustainability has become a significant driver of innovation in 3D printed injection molds. Use of biodegradable materials and recyclable 3D printing materials in injection molds to make the manufacturing process more environmentally friendly.
Integration with Industry 4.0:
The integration of 3D printing technology with Industry 4.0 is set to accelerate the adoption of 3D printed injection molds in manufacturing. Sensors are being used to monitor mold quality in real-time, and AI algorithms are being used for predictive maintenance.
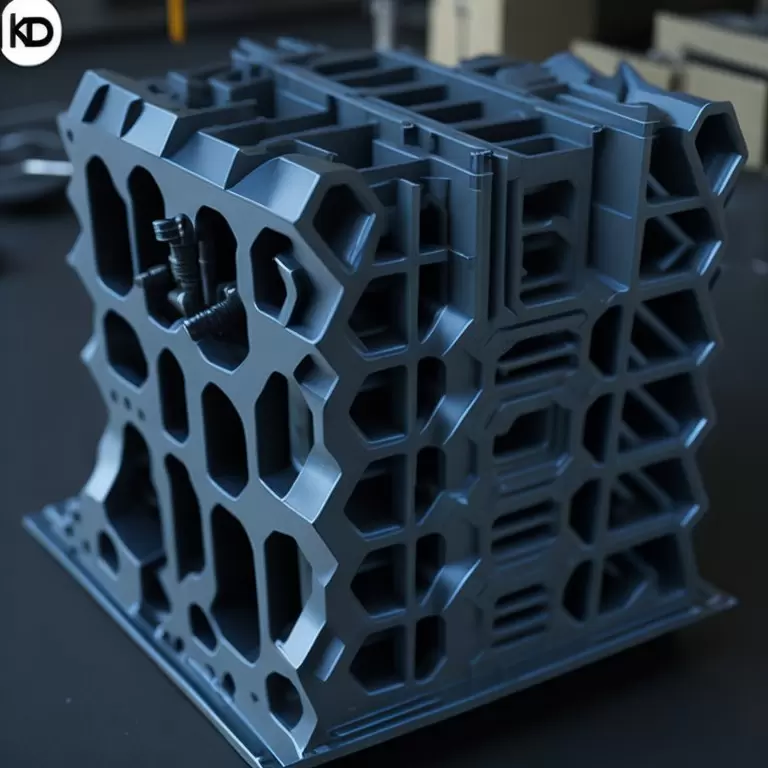
-
7.Comparison between 3D Printed Injection Molds and Other Mold Making Methods
Comparison with Traditional Injection Molding:
Traditional injection molding processes have higher production capacities than 3D printed injection molds due to their high pressure and temperature capabilities. However, they require higher upfront tooling costs, longer lead times, and are not suitable for small production batches.
Comparison with Other 3D Printed Molds:
Compared to other 3D printed molds such as silicone, 3D printed injection molds provide higher accuracy and can withstand higher temperatures and pressures. They also offer a faster turnaround time than silicone molds.
If you need about 3D Printing Services,You can click on the V1 Prototype website to find it.
-
8. Conclusion:
3D printed injection molds offer the manufacturing industry a compelling new advantage by combining the flexibility and customization of 3D printing with the precision and speed of injection molding. While there are still limitations, the growing availability of new materials and expanding capabilities of 3D printing technology are continuing to drive advancements in the process. As with any innovative technology, there are opportunities and challenges. However, it is through exploring these opportunities and confronting these challenges that we see the value and potential of 3D printed injection molds in the years to come.