Table of Contents:
- Introduction
- Types of Injection Moulding Machines
- Applications of Injection Moulding Machines
- Factors to Consider in Choosing an Injection Moulding Machine
- Conclusion
-
1.Introduction
The injection moulding process involves the melting of plastic granules and injecting the melted plastic into a mould to form a specific shape and size. This process is widely used in various industries due to its efficiency, versatility, and accuracy.
Injection moulding machines are the backbone of the injection moulding process. They are responsible for heating and melting the plastic granules, injecting it into the mould and then ejecting the final product. The importance of these machines in the manufacturing process cannot be overstated, as they play a vital role in determining the overall quality and efficiency of the production process.
In the following sections, we will explore the different types of injection moulding machines, their applications, and the factors to consider when choosing the right machine for a specific production requirement.
-
2.Types of Injection Moulding Machines
A. Hydraulic Injection Moulding Machines:
- Working Principle:
Hydraulic injection moulding machines use hydraulic oil to control the mechanical movements of the machine. The hydraulic system controls the pressure, flow and direction of the oil to determine the speed, force and movement of the mechanisms that push the plastic into the mould. - Advantages:
- Suitable for processing a wide range of materials
- Reliable and durable
- Low initial cost compared to other types of injection moulding machines
- Disadvantages:
- High energy consumption due to the use of hydraulic oil
- Slow cycle times compared to newer technologies
- High maintenance requirements due to the complexity of the hydraulic systems
.
B. Electric Injection Moulding Machines:
- Working Principle:
Electric injection moulding machines use electric motors to control the movements of the machine. The motors control the pressure, speed and direction of the mechanisms that push the plastic into the mould. - Advantages:
- High precision and repeatability
- Energy efficient
- Fast cycle times
- Disadvantages:
- Limited to processing certain materials
- Higher initial cost compared to hydraulic machines
- Less durable than hydraulic machines
.
C. Hybrid Injection Moulding Machines:
- Working Principle:
Hybrid injection moulding machines combine the best features of hydraulic and electric machines. They use electric motors to control the movements of the machine, but have a hydraulic system that provides additional support and power when needed. - Advantages:
- Energy efficient
- High precision and repeatability
- Fast cycle times
- Suitable for processing a wide range of materials
- Disadvantages:
- Higher initial cost compared to traditional hydraulic machines
- Maintenance requirements may be higher due to combined hydraulic and electric systems
.
D. Two-Shot Injection Moulding Machines:
- Working Principle:
Two-shot injection moulding machines have two injection units that can inject two different materials simultaneously or sequentially into the same mould. - Advantages:
- Can produce complex parts with multiple materials
- Reduces assembly time and costs by producing multi-component parts in one step
- Offers more design flexibility for product development
- Disadvantages:
- Higher initial cost compared to traditional injection moulding machines
- Requires careful consideration of part design and material selection for successful production
-
3.Applications of Injection Moulding Machines
Injection moulding machines are used in a wide range of industries due to their versatility, efficiency, and accuracy. Here are some common applications of injection moulding machines:
- Automotive - Injection moulding machines are used to produce a variety of car parts, such as instrument panels, bumpers, and interior trim components. The high production speed and accuracy of injection moulding ensures consistent quality and reduces production costs.
- Medical - Injection moulding machines are used to produce medical devices ranging from disposable syringes to more complex instruments such as cardiac catheters. The use of sterile and disposable medical devices produced by injection moulding machines helps to minimize the spread of infection in hospitals and medical facilities.
- Packaging - Injection moulding is commonly used to produce packaging products such as bottles, caps, and containers. The lightweight, durable and easily mass-produced nature of these products make them ideal for a range of industries including food, pharmaceuticals, and cosmetics.
- Consumer appliances - Injection moulding machines are used to produce various components of consumer appliances like coffee makers, toasters, blenders and more. The high production speed and accuracy of injection moulding ensure reliable and consistent component quality.
- Others - Injection moulding machines are also used in various industries such as electronics, toys, construction, and aerospace.
In each application, injection moulding machines play an important role in the production process by providing fast and precise manufacture of complex parts in large quantities at an affordable cost.
If you need about Injection Moulding Services,You can click on the V1 Prototype website to find it.
-
4.Factors to Consider in Choosing an Injection Moulding Machine
Selecting the right injection moulding machine is critical to the success of the production process. Here are some essential factors to consider when choosing an injection moulding machine:
- Material: The type of material used in the production process plays a significant role in the type of injection moulding machine required. For example, materials such as thermoplastics, thermosetting plastics, and elastomers require different temperature and pressure conditions and may require specific machinery.
- Production volume: The production volume required determines the size and output of the machine. High volume production requires a larger and more powerful machine to cater to the increased demand.
- Precision requirements: The level of precision required in the production process determines the type of machine needed. For example, the use of electric injection moulding machines provides high precision and repeatability compared to hydraulic machines.
- Cost: Finally, the cost of the machine and associated maintenance and operating expenses should be considered. The initial investment should be weighed against the long-term costs, energy consumption, and maintenance required for the selected machine.
By considering these factors during the selection and configuration of injection moulding machines, one can choose the best machine for the production process.
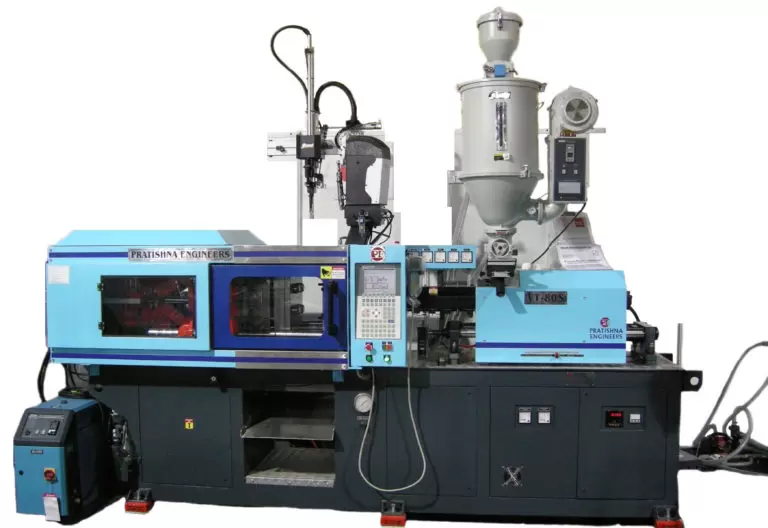
-
5.Conclusion
Injection moulding machines are an essential part of the manufacturing process and are widely used in various industries due to their versatility, efficiency, and accuracy.
Key points to consider when choosing an injection moulding machine include the type of material to be used, the required production volume, precision requirements, and the cost.
The future of injection moulding technology looks promising, with ongoing innovations in automation and Industry 4.0 technologies, such as artificial intelligence and the Internet of Things (IoT). These technologies are expected to increase the efficiency, precision, and automation of injection moulding processes.
Overall, injection moulding machines remain critical to the manufacturing process and future technological advancements in the field can only increase their importance in the years to come.