Table of Contents:
- Introduction
- The Plastic Injection Molding Process
- Types of Plastic Injection Molding Products
- Designing for Plastic Injection Molding
- Materials Used in Plastic Injection Molding
- Finishing Processes for Plastic Injection Molding Products
- Quality Control and Testing
- Sustainability in Plastic Injection Molding
- Future of Plastic Injection Molding Products
- Conclusion
-
1.Introduction
Plastic injection molding is a manufacturing process that involves injecting molten plastic material into a mold cavity under high pressure. Once the material cools and solidifies, it takes the shape of the mold cavity and forms a solid plastic part. This process is widely used for mass-producing high-quality, complex plastic parts with excellent dimensional accuracy and repeatability.
There are several advantages to using plastic injection molding for manufacturing products. First, it allows for the production of high volumes of parts with consistent quality and precision. The process is also highly efficient, with minimal waste and a short cycle time. Additionally, plastic injection molding can produce parts with a wide range of shapes, sizes, and complexities, making it a versatile manufacturing method for a variety of industries.
Plastic injection molding products are used in numerous applications, including automotive parts, medical devices, consumer goods, packaging products, and electrical and electronic products. The ability to produce high-quality, complex parts with consistent quality and precision has made plastic injection molding an essential manufacturing process for many industries.
-
2.The Plastic Injection Molding Process
The plastic injection molding process involves several steps that must be carefully executed to produce high-quality parts. The steps of the process are as follows:
- Material Selection: The first step is to select the appropriate plastic material for the desired part. Factors to consider include the material’s strength, flexibility, temperature resistance, and chemical compatibility.
- Melting and Injection: The plastic material is melted and injected into the mold cavity under high pressure using an injection molding machine. The mold is designed to have the desired shape of the final part.
- Cooling and Solidification: The plastic material is allowed to cool and solidify in the mold cavity. Cooling time is critical as it affects the part’s quality, strength, and dimensional accuracy.
- Ejection: Once the plastic has solidified, the mold is opened, and the part is ejected.
- Finishing: The part may require post-processing operations such as trimming, drilling, or machining to achieve the desired finish.
There are several types of plastic injection molding machines, including hydraulic, electric, and hybrid machines. Hydraulic machines are the most commonly used and are ideal for producing large parts with high clamping forces. Electric machines are more energy-efficient and produce less noise, making them suitable for smaller parts. Hybrid machines combine the benefits of both hydraulic and electric machines.
Several factors affect the plastic injection molding process, including the material used, mold design, temperature, pressure, cooling time, and injection speed. These factors must be carefully controlled to ensure that the final product meets the required specifications.
-
3.Types of Plastic Injection Molding Products
Plastic injection molding products are used in a wide range of industries and applications. Here are some of the most common types of plastic injection molding products:
- Automotive Parts: Plastic injection molding is widely used to manufacture various automotive parts, such as dashboards, bumpers, door panels, and interior trims. Plastic parts are lighter and more cost-effective than metal parts, making them ideal for reducing vehicle weight and improving fuel efficiency.
- Medical Devices: Many medical devices, such as syringes, tubing, and housings for electronic medical devices, are made using plastic injection molding. The process allows for the production of complex, high-precision parts with consistent quality and sterilization.
- Consumer Goods: Plastic injection molding is used to manufacture a variety of consumer goods, such as toys, kitchenware, and personal care products. The process allows for the production of colorful, high-quality parts with a smooth finish.
- Packaging Products: Many plastic packaging products, such as bottles, caps, and containers, are made using plastic injection molding. The process allows for the production of lightweight, durable packaging with consistent quality and precision.
- Electrical and Electronic Products: Many electrical and electronic products, such as connectors, switches, and housings for electronic devices, are made using plastic injection molding. The process allows for the production of high-precision, high-quality parts with excellent electrical insulation and heat resistance.
-
4.Designing for Plastic Injection Molding
Designing plastic parts for injection molding requires careful consideration of several factors to ensure that the final product meets the required specifications. Here are some key considerations for designing plastic injection molded parts:
- Wall Thickness: Parts with uniform wall thickness allow for even material flow during injection molding and reduce the risk of defects such as warping and sink marks.
- Draft Angles: Draft angles are critical to allow for the easy ejection of the part from the mold. A draft angle of at least 1-2 degrees is recommended.
- Ribs and Bosses: The use of ribs and bosses can add strength and rigidity to the part while reducing material and manufacturing costs.
- Surface Finish: The surface finish of the part is important for its appearance and functionality. Mold texture, gating location, and gate size can affect the surface finish of the part.
Common design mistakes to avoid include sharp corners, undercuts, and insufficient draft angles. These design features can make it difficult to manufacture the part and increase the risk of defects.
Prototyping and testing are essential steps in the plastic injection molding design process. Prototyping allows for the testing of the design for functionality, fit, and form before committing to mass production. Testing involves using simulation software and physical testing to optimize the design and manufacturing process.
-
5.Materials Used in Plastic Injection Molding
The material used in plastic injection molding plays a critical role in the final product’s performance, cost, and functionality. Here are some of the key aspects of materials used in plastic injection molding:
- Thermoplastics vs Thermosets: Thermoplastics and thermosets are the two main types of materials used in plastic injection molding. Thermoplastics can be melted and reformed multiple times, while thermosets cannot be remolded once they have been set. Thermoplastics are more commonly used in plastic injection molding due to their versatility and recyclability.
- Commonly Used Thermoplastics: Some of the most commonly used thermoplastics in plastic injection molding include polypropylene, polystyrene, ABS (Acrylonitrile Butadiene Styrene), PC (Polycarbonate), and nylon. Each of these materials has unique properties, such as strength, flexibility, chemical resistance, and temperature resistance, that make them suitable for specific applications.
- Material Properties and Selection: Material properties, such as tensile strength, elongation, and impact resistance, are critical factors in selecting the appropriate material for a plastic injection molding application. The material must also be compatible with the manufacturing process and the final product’s requirements, such as color, surface finish, and dimensional accuracy. The selection of the appropriate material can help reduce manufacturing costs, improve product performance, and enhance the product’s aesthetics.
Overall, selecting the appropriate material for a plastic injection molding application requires careful consideration of the product’s requirements, manufacturing process, and end-use environment.
-
6.Finishing Processes for Plastic Injection Molding Products
After the plastic injection molding process, the plastic parts may require additional finishing processes to enhance their aesthetics, functionality, and durability. Here are some of the most common finishing processes for plastic injection molding products:
- Surface Finishing Techniques: Surface finishing techniques are used to improve the appearance and texture of the part. Common surface finishing techniques include painting, texturing, and polishing. Painting can add color and protect the part from the environment. Texturing can create a specific surface finish, such as a matte or glossy finish, while polishing can create a smooth surface finish.
- Post-Molding Operations: Post-molding operations may be required to remove excess material or improve the part’s dimensional accuracy. Common post-molding operations include trimming, drilling, and machining. Trimming involves removing any excess material from the part, while drilling and machining are used to create specific features or holes.
- Assembly and Packaging: Assembly and packaging may be required for plastic injection molded parts to be ready for use. Assembly may involve joining multiple parts together, such as snap-fits or adhesive bonding. Packaging may involve placing the part in a protective container or wrapping to protect it from damage during transportation and storage.
Overall, finishing processes for plastic injection molding products can enhance their aesthetics, functionality, and durability. Careful consideration of these processes can help ensure the final product meets the required specifications and end-use requirements.
-
7.Quality Control and Testing
Quality control and testing are critical steps in the plastic injection molding process to ensure that the final product meets the required specifications and quality standards. Here are some key aspects of quality control and testing for plastic injection molding products:
- Inspection and Testing Methods: Inspection and testing methods can help detect defects and ensure that the final product meets the required specifications. Common inspection and testing methods for plastic injection molding products include visual inspection, dimensional measurement, material testing, and performance testing.
- ISO Standards for Plastic Injection Molding Products: ISO (International Organization for Standardization) standards provide guidelines for the design, manufacturing, and testing of plastic injection molding products. The ISO 9001 standard outlines requirements for a quality management system, while the ISO 13485 standard outlines requirements for medical device manufacturing.
- Common Defects and Solutions: Common defects in plastic injection molding products include sink marks, warpage, flash, and short shots. Sink marks and warpage can be caused by improper material selection, poor part design, or inadequate cooling. Flash and short shots can be caused by issues with the mold design or manufacturing process. Solutions to these defects may involve adjusting the mold design, optimizing the manufacturing process, or selecting a different material.
Overall, quality control and testing are critical aspects of plastic injection molding to ensure that the final product meets the required specifications and quality standards. Inspection and testing methods, ISO standards, and solutions to common defects can help improve product quality and performance.
-
8.Sustainability in Plastic Injection Molding
Sustainability is a growing concern in the plastic injection molding industry due to the environmental impact of plastic waste. Here are some key aspects of sustainability in plastic injection molding:
- Environmental Impact of Plastic Injection Molding: Plastic injection molding contributes to environmental pollution through greenhouse gas emissions, energy consumption, and waste generation. The use of non-biodegradable plastics can also lead to ocean pollution and harm to wildlife.
- Sustainable Materials and Practices: The use of sustainable materials, such as biodegradable plastics or recycled materials, can help reduce the environmental impact of plastic injection molding. Sustainable practices, such as optimizing the manufacturing process to reduce waste and energy consumption, can also help minimize the environmental impact.
- Recycling and Upcycling of Plastic Injection Molding Products: Recycling and upcycling of plastic injection molding products can help reduce waste and conserve resources. Recycling involves converting plastic waste into new products, while upcycling involves using waste materials to create products of higher value.
Overall, sustainability in plastic injection molding requires a holistic approach that considers the environmental impact of the entire manufacturing process, from material selection to waste management. The use of sustainable materials and practices, as well as recycling and upcycling of plastic injection molding products, can help reduce the environmental impact and move towards a more sustainable future.
-
9.Future of Plastic Injection Molding Products
The future of plastic injection molding products is shaped by emerging technologies and trends, new materials and applications, as well as challenges and opportunities. Here are some key aspects of the future of plastic injection molding:
- Emerging Technologies and Trends: Emerging technologies and trends in plastic injection molding include Industry 4.0, which involves the use of digital technologies to optimize the manufacturing process, such as predictive maintenance and real-time monitoring. Other emerging technologies include 3D printing, robotics, and automation.
- New Materials and Applications: New materials and applications for plastic injection molding products are constantly being developed. Biodegradable plastics, sustainable materials, and high-performance plastics are some examples of new materials being used in plastic injection molding. New applications for plastic injection molding products include medical devices, aerospace components, and automotive parts.
- Challenges and Opportunities: Challenges facing the plastic injection molding industry include the environmental impact of plastic waste and the need for sustainable practices. Other challenges include supply chain disruptions, rising raw material costs, and increasing competition. However, opportunities also exist, such as the growing demand for lightweight and high-performance materials, the expansion of the automotive and medical industries, and the increasing focus on sustainability.
Overall, the future of plastic injection molding products is shaped by emerging technologies and trends, new materials and applications, as well as challenges and opportunities. Continued innovation, sustainability, and adaptability to changing market demands will be critical for the success of the plastic injection molding industry in the future.
Click on the V1 Prototype website to gain more Plastic Injection Molding Services information.
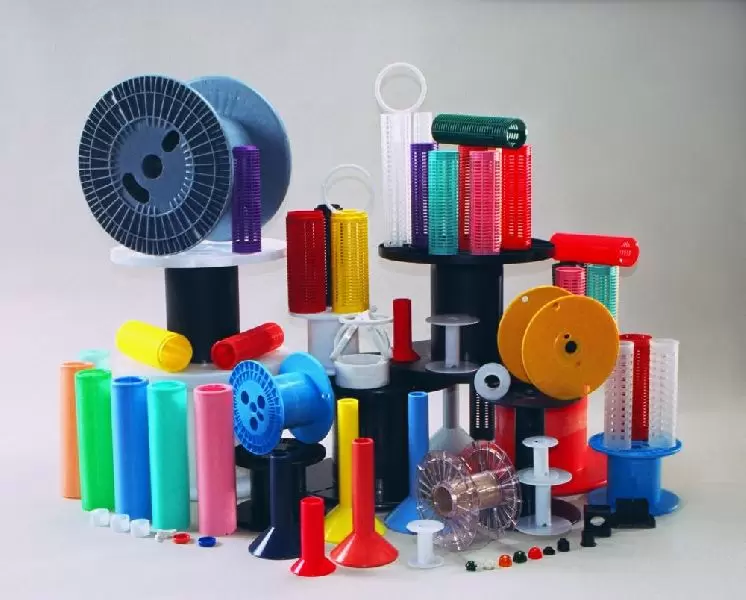
-
10.Conclusion
In conclusion, plastic injection molding is a versatile and widely used manufacturing process that produces a variety of products, including automotive parts, medical devices, consumer goods, packaging products, and electrical and electronic products. The plastic injection molding process involves several steps, including material selection, mold design, and finishing processes, and requires careful consideration of design and material properties.
The importance of plastic injection molding products lies in their widespread use and the benefits they provide, such as cost-effectiveness, versatility, and design flexibility. However, the environmental impact of plastic waste and the need for sustainable practices pose challenges for the industry.
Looking to the future, the plastic injection molding industry must continue to innovate and adapt to changing market demands, while also prioritizing sustainability and reducing the environmental impact of plastic waste. Emerging technologies and trends, new materials and applications, and challenges and opportunities will shape the future of plastic injection molding products.
Overall, plastic injection molding products will continue to play a significant role in various industries and applications, and their importance and impact will only increase as the industry moves towards a more sustainable and innovative future.
Plastic injection molding is a process that transforms plastic pellets or granules into various shapes and sizes of products. It is widely used in many industries, such as automotive, medical, aerospace, consumer goods, and more. In this blog post, we will explain the basics of plastic injection molding, the advantages and disadvantages of this method, and some examples of plastic injection molding products.
What is plastic injection molding?
Plastic injection molding is a manufacturing technique that involves heating plastic material until it melts and then injecting it into a mold cavity under high pressure. The mold cavity is a hollow shape that matches the desired product. The plastic material fills the mold cavity and cools down, forming the product. The mold is then opened and the product is ejected.
The plastic injection molding process consists of four main stages:
- Clamping: The mold is closed and clamped by a hydraulic or mechanical force.
- Injection: The plastic material is fed into a heated barrel, where it melts and becomes a viscous fluid. A screw or plunger pushes the molten plastic into the mold cavity through a nozzle.
- Cooling: The plastic material solidifies inside the mold cavity as it cools down. The cooling time depends on the thickness and shape of the product, as well as the type of plastic material used.
- Ejection: The mold is opened and the product is ejected by a mechanism such as ejector pins or air blast.
What are the advantages and disadvantages of plastic injection molding?
Plastic injection molding has many advantages over other methods of producing plastic products, such as:
- High efficiency: Plastic injection molding can produce large quantities of products in a short time, as each cycle takes only a few seconds to minutes. It also reduces waste and scrap, as the excess plastic material can be reused or recycled.
- High quality: Plastic injection molding can produce products with complex shapes, fine details, and high dimensional accuracy. It also allows for a wide range of colors, finishes, and textures to be applied to the products.
- Low cost: Plastic injection molding can reduce the cost of production by using less material, energy, and labor. It also reduces the need for secondary operations, such as trimming, drilling, or painting.
However, plastic injection molding also has some disadvantages, such as:
- High initial investment: Plastic injection molding requires expensive equipment, such as injection machines, molds, and auxiliary devices. The molds are custom-made for each product and can be costly to design and manufacture.
- Limited flexibility: Plastic injection molding is suitable for mass production of products with fixed shapes and sizes. It is not easy to change the design or specifications of the products once the molds are made. It also limits the types of plastic materials that can be used, as they have to withstand high temperatures and pressures.
- Environmental impact: Plastic injection molding can generate harmful emissions, such as volatile organic compounds (VOCs), carbon dioxide (CO2), and particulate matter (PM). It also contributes to the problem of plastic pollution, as some plastic products are not biodegradable or recyclable.
What are some examples of plastic injection molding products?
Plastic injection molding products are everywhere in our daily lives. Some common examples are:
- Automotive parts: Plastic injection molding can produce various parts for cars, such as bumpers, dashboards, door handles, headlights, and taillights.
- Medical devices: Plastic injection molding can produce various devices for medical purposes, such as syringes, catheters, implants, surgical instruments, and test tubes.
- Aerospace components: Plastic injection molding can produce various components for aerospace applications, such as wings, fuselages, propellers, and landing gears.
- Consumer goods: Plastic injection molding can produce various goods for consumers, such as toys, bottles, containers, utensils, appliances, and electronics.
Plastic injection molding is a versatile and efficient method of producing plastic products. It has many benefits in terms of quality, quantity, and cost. However, it also has some drawbacks in terms of flexibility and environmental impact. Therefore, it is important to consider these factors when choosing plastic injection molding for your project.