Table of Contents:
- Introduction
- Raw Materials Used in Plastic Manufacturing
- Plastic Manufacturing Processes
- Quality Control in Plastic Manufacturing
- Design Considerations for Plastic Products
- Environmental Impact of Plastic Manufacturing
- Conclusion
-
1.Introduction
As a highly versatile material, plastic has become an integral feature of our everyday lives. From consumer goods and packaging to automotive and medical devices, plastic finds widespread use in a range of industries due to its light weight, affordability, and durability. However, with the many benefits plastic provides come a variety of manufacturing challenges. Understanding the plastic manufacturing process, from raw material selection to design considerations and environmental impacts, is critical to ensuring the production of high-quality plastic goods. In this article, we will delve into the key aspects of plastic manufacturing, providing an overview of the process and its significance in modern manufacturing.
-
2.Raw Materials Used in Plastic Manufacturing
The primary raw materials used in plastic manufacturing are polymers, which are long chains of repeating molecules. There are several types of plastics, each with its own unique set of properties and production processes.
Some commonly used types of plastics include:
- Polyethylene (PE) – the most widely used plastic in the world due to its low cost and wide range of applications.
- Polypropylene (PP) – a versatile plastic commonly used in packaging, textiles, and automotive applications.
- Polyvinyl chloride (PVC) – a durable, weather-resistant plastic used in construction, electrical and medical applications.
- Polystyrene (PS) – a lightweight, rigid plastic used in packaging and insulation.
- Polyethylene terephthalate (PET) – a strong, clear plastic used in food and beverage packaging.
.
The properties of the raw materials used in plastic manufacturing vary widely depending on the type of plastic. Some of the key properties include:
- Melting point: the temperature at which the plastic melts and can be shaped into the desired form.
- Density: the mass per unit volume of the plastic.
- Tensile strength: the ability of the plastic to resist breaking under tension.
- Flexural strength: the ability of the plastic to resist bending.
- Chemical resistance: the ability of the plastic to resist degradation from exposure to chemicals.
Understanding the properties of the raw materials is essential in selecting the appropriate plastic for a particular application and in designing the manufacturing process.
-
3.Plastic Manufacturing Processes
Plastic manufacturing processes involve a range of techniques for shaping and forming polymers into final products. Here are key examples of plastic manufacturing processes:
- Extrusion: An extrusion process involves forcing melted plastic through a die to create a continuous profile or shape, such as tubes, pipes, and sheets. This process is commonly used in the production of plastic bags, films, and packaging materials.
- Injection Molding: Injection molding is a popular process for creating plastic parts in large quantities with high precision. Molten plastic is injected into a mold cavity under high pressure and allowed to cool and solidify before the finished part is ejected from the mold.
- Blow Molding: Blow molding is a method for creating hollow plastic parts, such as bottles and containers. Molten plastic is extruded into a cavity, and then air is blown into the cavity to expand the plastic and form the desired shape.
- Rotational Molding: Rotational molding is a process of heating plastic powders within a rotating mold to produce large parts with uniform wall thicknesses, such as tanks and drums. The rotating action ensures that the plastic is evenly distributed throughout the mold.
- Thermoforming: Thermoforming involves heating a plastic sheet until it becomes pliable and then shaping it by vacuum-forming it over a mold. This process is commonly used in the production of product packaging, trays, and containers.
These processes are applicable to different types of plastics and a wide range of applications. Each method has its distinct capabilities and limitations, and selecting the right one for a specific application depends on factors like part geometry, material properties and production volumes.
-
4.Quality Control in Plastic Manufacturing
As with any manufacturing process, quality control is crucial in plastic manufacturing to ensure that the finished products meet the desired specifications. Here are some aspects of quality control in plastic manufacturing:
- Testing Procedures: There are numerous testing procedures that manufacturers can use to evaluate the quality of the raw materials, the intermediate products, and the final product. Tests include visual inspection, dimensional measurement, tensile strength testing, chemical and thermal analysis, and various non-destructive testing methods.
- Approaches to Maintenance: Regular maintenance of equipment is essential in minimizing downtime, maximizing productivity, and ensuring product quality. Maintenance includes cleaning, calibration, replacement of consumable parts, and monitoring of critical parameters.
- Process Improvement Techniques: To continually improve the quality of the product and the efficiency of the manufacturing process, manufacturers use a variety of techniques. Such techniques include statistical process control (SPC), which uses statistical methods to monitor and control the process and identify sources of variation. Six Sigma methodology, which aims to reduce the defects in the manufacturing process, is also common.
Regardless of the specific quality control strategy used, manufacturers must continuously monitor the process and products to detect and address any quality issues early on. This approach ensures that products adhere to industry standards, meet customer requirements, and minimize waste and rework.
-
5.Design Considerations for Plastic Products
Designing plastic products that meet specific requirements and perform as expected involves careful consideration of several factors. Here are some key design considerations:
- Mold Design: The mold is a critical component, which defines the final shape and quality of the product. Designing a mold that matches the part geometry and the manufacturing process is crucial. Considerations, including surface finish, cooling time, parting lines, and potential shrinkage of the plastic in the mold.
- Part Design: Design considerations for the part itself include characteristics like wall thickness uniformity, rib designs, and the placement of the gate (the point through which molten plastic is injected into the mold). Designing with injection molding in mind would be to minimize the number of undercuts, design to avoid thin steeling parts and consider design options that improve mold release.
- Material Selection: Selecting the appropriate plastic materials for a specific application is important since it impacts factors such as mechanical properties, durability, weight, and temperature resistance. Considering aspects such as the application process used and the environmental conditions surrounding the product is critical in choosing appropriate materials such as medical grade class IV or if the resin used is bio-degradable hence aligning with sustainability goals of organizations.
Effective collaboration between the design and manufacturing departments, using modeling software and virtual tests, is critical in ensuring that the final product meets design specifications and manufacturing feasibility.
-
6.Environmental Impact of Plastic Manufacturing
The environmental impact of plastic manufacturing remains a significant concern, and measures to mitigate that impact have been developed over time. Here are some key considerations:
- Recycling and Waste Management: Because of the durability of plastics, they remain in the environment for extended periods, leading to contamination, depletion of resources, and littering. Efficient recycling and waste management are essential in decreasing the environmental impact of plastic manufacturing. Options such as mechanical and chemical recycling and repurposing of materials for products like plastic lumber or fibers are becoming more popular.
- Sustainability Initiatives: Businesses are taking a proactive role in the creation of sustainable initiatives that aims to improve the environmental impact of plastic manufacturing. These measures include developing eco-friendly plastics, using sustainable packaging, and adopting circular economic principles to address the challenge of single-use plastics. Design practices, such as reducing the amount of plastic used by lightweighting or using more environmentally friendly alternatives such as paper, bamboo or reusable containers, and increased materials recovery aimed at reducing wastage.
- Government Regulations: Governments in several countries have implemented rules aimed at controlling the impact of plastic manufacturing on the environment. Some of the regulations include the prohibition of single-use plastics, imposing taxes and fees on plastics, encouraging the use of sustainable materials and methods, and the introduction of standardized labeling and recycling programs to promote recycling and waste management.
By adopting environmentally-friendly manufacturing practices, businesses can improve their products’ sustainability profiles, better align with their customers’ expectations, and comply with the relevant regulations.
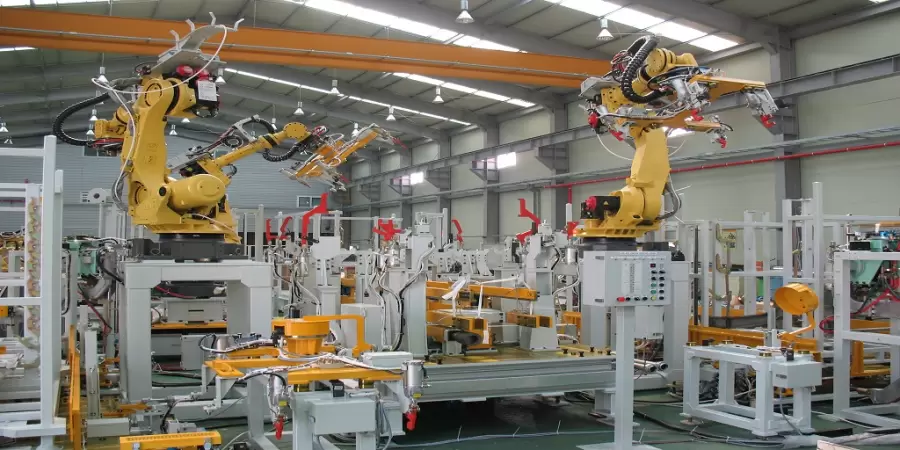
-
7.Conclusion
Plastic manufacturing is a vital aspect of modern manufacturing and has revolutionized various industries by allowing them to produce lightweight, durable, and affordable products. As with any manufacturing process, quality control is critical, and manufacturers must continually monitor and refine their processes to ensure the products meet the required specifications.
While plastic manufacturing has many benefits, it is crucial to recognize its environmental impact and take proactive measures to mitigate that impact. Businesses should invest in sustainable manufacturing practices, such as effectively recycling and managing waste, using sustainable materials and methods, and researching new eco-friendly options.
In conclusion, plastic manufacturing is critical for modern industry and manufacturing, and understanding its key elements is crucial for creating quality products while minimizing the environmental impact. By balancing the importance of plastic manufacturing with the need for sustainability, businesses can continue to expand their operations while contributing to a more sustainable future.