Table of Contents:
- Introduction to Injection Parts
- Materials Used in Injection Parts
- Injection Molding Process
- Injection Molding Machines and Tooling
- Quality Control for Injection Parts
- Applications of Injection Parts
- Design Considerations for Injection Parts
- Future Developments in Injection Parts
- Conclusion
-
1.Introduction to Injection Parts
Injection parts refer to various plastic components that are produced using the injection molding process. Injection molding is a manufacturing method used in the production of parts in large quantities. It involves melting plastic resin or material, injecting it into a mold, and allowing the material to cool and solidify to form the desired shape. This process provides a cost-effective way of producing injection parts with high volume and precision.
Injection parts can be found in various industries, including the automotive, medical, consumer goods, and electronics industries. The process allows for the production of intricate and detailed designs with high accuracy, making it a popular manufacturing method.
-
2.Materials Used in Injection Parts
Injection parts are produced from different types of plastic resins or materials, depending on the needed properties and application of the final product. The following are the most commonly used plastic resins in injection molding:
- Polypropylene (PP): This is a thermoplastic polymer that is lightweight and has high hardness, toughness, and stiffness. It is used to produce products such as flip-top bottles, crates, and automotive parts.
- Acrylonitrile Butadiene Styrene (ABS): This is a tough and rigid thermoplastic polymer that is used to produce automotive parts, toys, and computer equipment.
- Polyvinyl Chloride (PVC): This is a thermoplastic polymer that is used in the production of pipes, electrical cables, and footwear. It has good insulating properties and is resistant to chemicals.
- Polyethylene Terephthalate (PET): This is a type of thermoplastic polymer that is commonly used in the production of beverage bottles due to its clarity and ease of processing.
.
In addition to plastic resins, additives are often used during the injection molding process. Additives are introduced into the material to improve specific properties such as stability, color, strength, and resistance to fire. The following are some examples of additives used in the injection molding process:
- Stabilizers: These reduce the degradation of the material and improve the lifespan of the final product.
- Colorants: These are used to add color to the plastic resin and enhance the visual appeal of the finished product.
- Reinforcing agents: These are added to improve the mechanical properties of the finished product. Examples include glass fibers, carbon fibers, and mineral fillers.
- Flame retardants: These additives reduce the flammability of the material, making it safer for use in specific applications.
In conclusion, injection parts are made from various plastic resins and require the right additives to suit the particular application. The selection of a plastic resin and the right combination of additives used in injection molding manufacture will ultimately determine the final product’s quality, appearance, and durability.
-
3.Injection Molding Process
The injection molding process involves several key components and elements that are critical to the process’s success. In this section, we will explore these components, the various types of injection molding processes, and their variations.
Key Components of the Injection Molding Process
- Injection Unit: This component is tasked with melting and preparing the plastic resin or material for injection into the mold. The injection unit comprises the hopper, barrel, screw, and nozzle.
- Clamping Unit: This component is responsible for firmly holding the mold in place during the injection molding process.
- Mold: The mold defines the shape and design of the finished part. Molds are made in two halves and are designed to be easily separated for part ejection.
- Ejector System: This component is used to remove the finished part from the mold. The ejector system typically comprises ejector pins, ejector plate, and the knockout rod.
.
Types of Injection Molding Processes
- Conventional Injection Molding: This is the most common type of injection molding process. A molten plastic is injected into a closed mold, where it takes on the shape of the mold. The mold is then opened, and the part is ejected.
- Overmolding: In this process, two or more different materials are molded together to form a single part. The process typically involves a first shot to create a substrate which is then molded over with the second shot in a different material.
- Insert Molding: This process involves inserting pre-made components, such as metal or plastic parts, into the mold. The plastic material is then injected around the insert to produce a single finished part.
.
Process Variations
- Gas-assisted Injection Molding: This variation of the injection molding process uses gas under high pressure to force the molten plastic away from the mold wall, resulting in a part with hollow sections or walls.
- Micro Injection Molding: This process is used to produce injection parts with incredibly small dimensions, often below one millimeter.
- Co-Injection Molding: This process involves the injection of two different plastic materials into a single mold simultaneously. This process is often used to provide a product with specific properties or unattainable characteristics in a single material.
In summary, the injection molding process requires a combination of key components to produce quality parts, including the injection unit, clamping unit, mold, and ejector system. There are various types of injection molding processes and process variations, giving manufacturers flexibility and creativity to produce products that meet specific requirements. The increasing technological advancements in injection molding processes have resulted in highly intricate designs and high-quality finished products.
-
4.Injection Molding Machines and Tooling
Injection molding machines are essential in producing high-quality injection parts. In this section, we will explore the types of injection molding machines available, factors to consider when selecting an injection molding machine, and mold tooling and design.
Types of Injection Molding Machines
- Hydraulic Injection Molding Machines: These machines are commonly used in the production of large injection parts because they provide high force and pressure.
- Electric Injection Molding Machines: This type of machine is increasingly becoming popular because it provides higher accuracy, faster cycle times, and energy efficiency compared to hydraulic machines.
- Hybrid Injection Molding Machines: These machines combine the benefits of electric and hydraulic machines, making them more efficient than hydraulic machines but less expensive than electric machines.
.
Factors to Consider When Selecting an Injection Molding Machine
- Injection Capacity: This is the maximum volume of molten material that the machine can inject into a mold at any given time.
- Clamp Force: This refers to the amount of force required to hold the mold closed while the injection process takes place.
- Shot Size: This refers to the amount of material injected into the mold in a single cycle.
- Material Compatibility: The machine must be compatible with the type of plastic resin or material used in the injection molding process.
- Production Efficiency: Factors such as cycle time and energy consumption can have a significant impact on the production efficiency of the injection molding process.
.
Mold Tooling and Design
Mold tooling and design are critical elements in the injection molding process as they determine the final shape and quality of the injection part. The following are some essential considerations in mold tooling and design:
- Gate Design: The gate is the opening through which molten material enters the mold. The size and location of the gate are crucial in determining the final quality of the injection part.
- Runner Design: The runner is the channel that carries the molten material from the gate to the cavities within the mold. Proper design of the runner ensures that the molten material reaches all parts of the mold and reduces incomplete filling or warpage.
- Ejector Pin Design: The ejector pins are used to remove the finished part from the mold after the injection process is complete. Proper design of the ejector pins ensures that they exert enough force to remove the part without causing any damage.
In conclusion, selecting the right injection molding machine is an important part of the injection molding process. Factors such as injection capacity, clamp force, shot size, material compatibility, and efficiency must be considered when selecting an injection molding machine. Proper mold tooling and design are also crucial to producing high-quality injection parts. The use of advanced manufacturing techniques, such as automation and Industry 4.0, has resulted in increased efficiency and improved quality in the injection molding process.
-
5.Quality Control for Injection Parts
Quality control is a critical aspect of the injection molding process. It involves inspection, testing, and evaluation of materials and finished products to ensure they meet the required specifications. In this section, we will explore the various quality control processes involved in the production of injection parts.
Inspection and Testing of Materials
The quality control process begins with the inspection and testing of raw materials. This ensures that the plastic resin or material used in the injection molding process is of the required quality and purity. The following are some of the tests and inspections carried out on materials:
- Visual Inspection: This involves the observation of the materials for any visible irregularities, such as discoloration, impurities, or warping.
- Weight and Density Test: This is used to determine the weight and density of the material used in the injection molding process.
- Melt Flow Index Test: This test measures the viscosity and flow rate of the material to ensure consistency and quality.
.
Production Monitoring and Control
The injection molding process must be monitored and controlled to ensure that the quality of the injection parts is maintained consistently. This is achieved through real-time monitoring using sensors and other quality control tools. The following are some of the quality control processes involved in the production monitoring and control:
- Process Monitoring: This involves the monitoring of various process variables such as temperature, pressure, and injection speed, to ensure that they remain within the specified range during the injection molding process.
- Statistical Process Control (SPC): This is a quality control technique that involves the use of statistical methods to monitor and control the injection molding process’s performance.
- Automated Inspection: This is achieved through the use of computer vision systems and sensors that detect and identify defects such as cracks, voids, and warping during the injection molding process.
.
Testing and Evaluation of Finished Products
The final stage of the quality control process involves testing and evaluation of the finished injection parts. This ensures that the parts meet the required specifications and are of the desired quality. The following are some tests and inspections carried out on finished products:
- Dimensional Inspection: This involves the measurement and verification of the part’s dimensions to ensure that they meet the specified tolerance.
- Mechanical Strength Testing: This involves testing the mechanical properties of the part, such as tensile strength and impact resistance, to ensure that they meet the specified requirements.
- Optical Inspection: This involves using optical instruments to inspect the part’s surface for any defects, such as scratches or foreign material.
In conclusion, the quality control process plays a crucial role in the production of high-quality injection parts. The process begins with the inspection and testing of raw materials and involves the monitoring and control of the injection molding process to ensure consistency and quality. Finally, the finished products undergo testing and evaluation to ensure that they meet the required specifications. Advanced quality control techniques such as automated inspection and statistical process control are increasingly becoming popular to improve quality control and production efficiency in the injection molding process.
-
6.Applications of Injection Parts
Injection parts have various applications in different industries, thanks to their versatility, durability, and the flexibility provided by the injection molding process. In this section, we will explore the use of injection parts in various industries.
The automotive industry is one of the biggest users of injection parts, thanks to the production speed and cost-effectiveness of the injection molding process. The industry uses injection parts to produce a wide range of automotive components, including exterior parts, interior parts, and under-the-hood components. Examples of the injection parts used in the automotive industry include bumpers, dashboards, steering wheels, and engine components.
The medical industry requires components that are durable, easy to clean, and can withstand the harsh chemicals used in sterilization processes. Injection parts are widely used in the medical industry due to their ability to meet these requirements. Medical components produced through the injection molding process include syringes, inhalers, blood-tubes, and catheter components.
Consumer Goods Industry
The consumer goods industry uses injection parts to produce a wide range of products that are both functional and visually appealing. Examples of the injection parts used in the consumer goods industry include toothbrushes, toys, packaging materials, and kitchen utensils. Injection Parts offer flexibility in design and consistency in mass-production that make them an ideal choice for consumer product manufacturing.
Electronics Industry
The electronics industry requires components that are durable, lightweight, and can withstand high temperatures, and injection parts are an excellent solution to meet these requirements. Injection parts produced for the electronics industry include computer components, cell phone components, and electronic housings.
In conclusion, injection parts offer a great deal of functionality, versatility, and durability, making them valuable in various industries. Their unique production speed and cost-effectiveness make them an ideal choice for mass production. The automotive, medical, consumer goods, and electronics industries have all reaped benefits from the valuable qualities of injection parts. With the use of the latest manufacturing technologies, injection parts’ potential for application in various areas is expected to grow further with increased design flexibility and more innovative features.
-
7.Design Considerations for Injection Parts
Designing injection parts requires careful consideration of various factors for optimal functionality and production efficiency. In this section, we explore some of the essential design considerations for injection parts.
Design for Manufacturability
Design for manufacturability (DFM) is an essential factor to consider when designing injection parts. DFM emphasizes designing the parts in such a way that they are easy to manufacture throughout the production process with minimal waste. Some of the DFM considerations for injection parts include:
- Minimize complexity: Reducing the complexity of the design can reduce production costs and increase production efficiency.
- Consider injection molding constraints: Taking into account the injection molding process requirements can help determine the best design for the part, taking into account the molding process’s limitations.
- Material selection: Proper materials selection will ensure that the injection parts can be efficiently produced and can withstand various environmental factors.
.
Tool and Mold Design Considerations
The design of injection molds and tools is a key aspect of the injection molding process that greatly influences the production efficiency and quality of injection parts. Proper tool and mold design can help reduce defects and improve quality. The following are some of the mold and tool design considerations for injection parts.
- Design molds for easy maintenance and repair: Tool and mold design should allow easy maintenance and repair during and after production.
- Optimize runner and gate designs: Proper optimization of gate and runner designs can help reduce cycle times and improve injection product quality.
- Cooling system design: Properly designed cooling systems can help reduce cycle times and improve consistency in product quality.
.
Material Selection for Injection Parts
Material selection for injection parts is an essential factor that affects the overall cost, functionality, and durability of the parts. Proper material selection should consider several factors, including:
- Material properties: Selecting materials with the appropriate physical and mechanical properties to meet functional and aesthetic requirements.
- Material availability and cost: Materials should be readily available and cost-effective for mass production.
- Environmental considerations: Environmental factors such as temperature, humidity, and UV exposure should be considered, as they can affect the material’s durability and structural stability.
In conclusion, designing injection parts requires several considerations, including design for manufacturability, tool, and mold design considerations, and material selection. Addressing these design considerations will help produce quality injection parts, reduce production waste, and keep production costs down. Innovative technologies like simulations, design validation, and virtual prototypes have reduced design errors and has helped manufacturers to come up with optimized designs for injection parts. The optimal choice of design ultimately depends on the component function, injection molding process requirements, and suitability to the industry.
-
8.Future Developments in Injection Parts
Injection parts have continued to evolve over the years, with new technologies and materials contributing to their developments. In this section, we explore some of the significant future developments in injection parts.
Advancements in Materials and Processes
Advancements in materials and processes are accelerating the evolution of injection parts. Additive manufacturing technology and composite materials have already become essential technologies in many industries. In terms of the injection molding process, advancements in 3D printing, multi-shot molding, and co-injection molding will result in the production of more complex parts with fewer defects, faster cycle times, improved surface finishes, and unique functionalities. The increased use of natural fibers and other sustainable materials for injection parts offers new opportunities to reduce carbon emissions, increase product durability, and reduce material waste.
Automation and Industry 4.0
Automation has already transformed many industries, and the injection molding industry is no exception. Advancement in robotics and smart manufacturing technologies have increased the production speed of injection parts while improving quality control. The implementation of Industry 4.0 in injection molding offers manufacturers a competitive edge by leveraging data analytics, machine learning, and IoT to improve production planning, supply chain management, and material usage. It presents an opportunity for manufacturers to efficiently manage production and reduce production costs throughout the production process.
Environmental and Sustainability Factors
Environmental and sustainability factors are major concerns in the manufacturing industry, including the injection molding industry. There is an increasing push toward producing injection parts that are more eco-friendly, use recycled materials, and reduce carbon emissions. With the introduction of environmentally-friendly injection molding technology, manufacturers can reduce energy usage, decrease waste, and improve the health of the ecosystem.
In conclusion, advancements in materials and processes, automation and Industry 4.0, and environmental and sustainability factors are major future developments in injection parts. Injection molding technology is continually evolving to meet future demands for many industries, from automakers to medical device companies. Manufacturers can stay ahead of the curve by adopting new technologies and materials, leveraging automation, and embracing sustainable practices throughout the entire production process. The future of injection parts is expected to be more efficient, more sustainable, and more functional than ever before.
If you need about Injection Parts,You can click on the V1 Prototype website to find it.
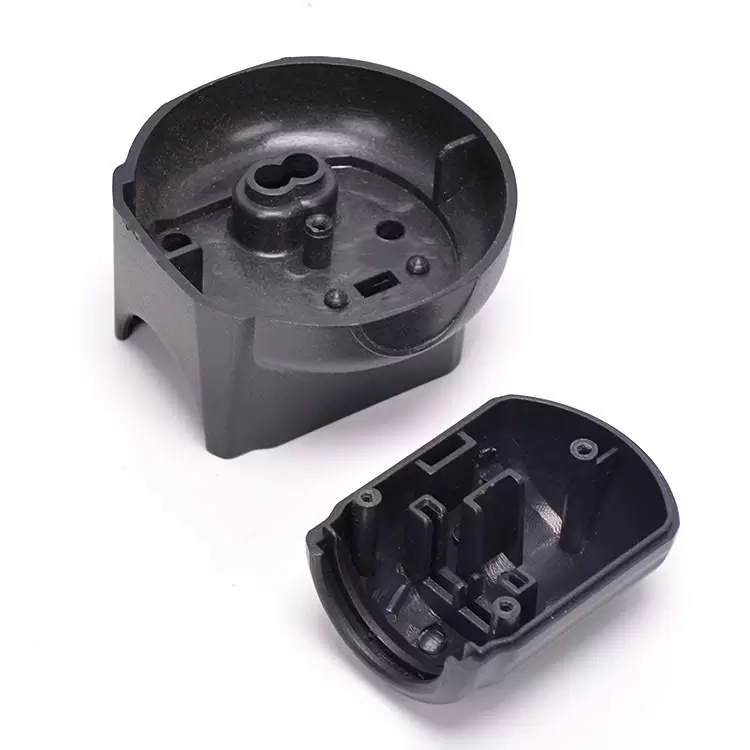
-
9.Conclusion
Injection parts are versatile, durable, and cost-effective components that find applications in various industries such as the automotive, medical, consumer goods, and electronics industries. These parts are manufactured through the injection molding process, which enables manufacturers to produce parts with complex geometries and design flexibility.
In this article, we have explored the key aspects of injection parts, including quality control, design, material selection, and future developments. We have seen that quality control is a critical aspect of the injection molding process to ensure that the parts meet the required specifications. Design is also essential for manufacturing purposes, and material selection should take into account the physical and mechanical properties, availability, cost, and environmental factors.
Looking ahead, the future developments in the injection parts industry appear promising, with advancements in materials and processes, increased automation through Industry 4.0, and environmental and sustainability factors. Through these advancements, we can expect to see more efficient, more sustainable, and more functional injection parts.
In conclusion, the versatility, durability, and low-cost production of injection parts make them an ideal solution for many industries’ production needs. With innovative approaches to materials, processes, and manufacturing practices, manufacturers can expect to produce even higher quality injection parts to meet the needs of their customers in the future.