Table of Contents:
- Introduction
- Injection Molding Tool Design
- Injection Molding Tooling Production
- Injection Molding Tool Maintenance
- Injection Molding Tool Optimization
- Injection Molding Tooling Costs
- Conclusion
-
1.Introduction
Injection molding tooling is a method widely used in the manufacturing industry to produce parts from thermoplastic materials. This process involves melting the plastic pellets and injecting the molten material into a mold cavity, where it cools and solidifies to form the final product. Injection molding tooling is an efficient and cost-effective way to mass-produce identical parts with high precision and accuracy. This guide aims to provide a comprehensive understanding of injection molding tooling, its design principles, production techniques, maintenance practices, optimization strategies, and costs.
Definition of Injection Molding Tool:Injection molding tooling refers to the complex set of tools and equipment used in the injection molding process to produce plastic parts. These tools can be made of various materials like steel, aluminum, or copper alloys and are designed to withstand high pressure, temperature, and wear. Injection molding tooling consists of two main components, the mold and the injection molding machine, both of which work together to produce the final product.
History of Injection Molding Tooling:The origins of injection molding can be traced back to the late 19th century when celluloid, a type of thermoplastic, was discovered. However, the first commercial injection molding machine was developed by John Wesley Hyatt in 1872, which used a plunger mechanism to inject the plastic material into a mold. Over the years, injection molding technology has evolved significantly, with the development of new materials, design software, and manufacturing techniques. Today, injection molding tooling is a core component of modern manufacturing, used extensively across various industries, including automotive, aerospace, consumer electronics, and medical devices.
-
2.Injection Molding Tool Design
Tooling Design Considerations:
The design of injection molding tooling is a critical factor that determines the quality, consistency, and productivity of the injection molding process. The following are some essential tooling design considerations:
- Part geometry: The tooling design should reflect the specific shape, size, and features of the part, including any undercuts or side actions.
- Material selection: The tooling materials should be chosen to match the properties of the plastic resin being used, and the process parameters like temperature and pressure.
- Gate location: The placement of the gate determines how the plastic material enters the mold cavity, affecting part quality, cycle time, and scrap rates.
- Cooling system: The cooling system within the tooling should be well-designed to ensure uniform cooling and consistent part quality.
- Ejector and alignment systems: A precise ejector and alignment system should be employed to avoid damage to the part, tooling, and machine.
.
Types of Injection Molding Tools:
There are various types of injection molding tools that can be used, depending on the part geometry, material, and production volume. Below are some common types of injection molding tools:
- Two-plate mold: the simplest and most widely used type of tooling, consisting of two plates that open and close to form the mold cavity and runners.
- Three-plate mold: similar to the two-plate mold, but with an additional plate that separates the runners and sprue from the part.
- Hot runner mold: used for high volume production, this type of tooling uses a heated manifold system to keep the plastic material in a molten state and eliminates the need for runners.
- Multi-cavity mold: used to produce multiple identical parts simultaneously, increasing efficiency and reducing costs.
.
Design and Build Standards:
Injection molding tooling is subject to strict design and build standards to ensure quality and consistency. These standards can vary depending on the industry, application, and material being used, but some common standards include:
- Design guidelines from injection molding machine manufacturers and resin suppliers
- Guidelines from industry associations like the Society of Plastics Engineers (SPE)
- ISO 9001 standards for quality management
- ASTM standards for materials and testing
Common Tooling Materials:
The choice of injection molding tooling material impacts the cost, durability, and performance of the tooling. Common materials used for tooling include:
- Steel alloys: such as H13, P20, and S7, are commonly used for high-pressure molding applications due to their high strength, wear resistance, and thermal conductivity.
- Aluminum alloys: offer good thermal conductivity and are lighter, faster, and less expensive than steel, but have lower strength and durability.
- Copper alloys: excel in high-temperature applications, but tend to be expensive and require special machining techniques.
- Beryllium copper alloys: offer superior wear resistance and thermal conductivity, but can be costly and pose a health risk if not handled correctly.
-
3.Injection Molding Tooling Production
Tooling Process Overview:
The production of injection molding tooling involves several stages, including design, fabrication, validation, and testing. The following is an overview of the tooling production process:
- Design: The tooling design is the first stage of the production process. Engineers use computer-aided design (CAD) software to design and model the mold and runners based on the part geometry, material, and production volume.
- Fabrication: Once the design is complete, the tooling is fabricated using a combination of machining, heat treating, and finishing techniques. This may involve CNC machining, electrical discharge machining (EDM), welding, polishing, and heat treatment to achieve the desired shape, surface texture, and strength.
- Validation: Once the tooling is fabricated, it is tested and validated to ensure it meets the design specifications, material properties, and production requirements. This may involve sample runs, dimensional and functional testing, and other quality control measures.
- Testing: After validation, the tooling undergoes final testing to ensure it is ready for production. This may involve installing the tooling on the injection molding machine, running full production cycles, and making necessary adjustments and repairs.
Tooling Fabrication Techniques:
The fabrication of injection molding tooling involves several techniques and processes, including:
- CNC machining: involves using computer-controlled machines to precisely cut and shape the tooling material.
- Electrical discharge machining (EDM): uses electrical discharges to remove material from the tooling surface, providing precise and intricate shapes.
- Welding: joins pieces of tooling material together to create complex geometries or repair damage.
- Polishing: provides a smooth and consistent surface finish, reducing friction and improving part quality.
- Heat treatment: improves the strength, durability, and wear resistance of the tooling material.
Tool Validation Process:
Validation is an essential step in the tooling production process to ensure the tooling meets the design specifications and requirements. The tool validation process typically involves:
- Preliminary mold tryout: The mold is tested before production to verify its dimensions and evaluate its performance.
- Mold sampling: A small batch of parts is produced using the mold to check its functionality, quality, and consistency.
- Inspection and testing: The molded parts are inspected for dimensional accuracy, surface finish, and any defects or imperfections.
- Final adjustments: Any necessary adjustments to the mold or process parameters are made to optimize its performance and ensure it is ready for production.
Common Challenges in Tooling Production:
The production of injection molding tooling can pose several challenges that impact the quality, consistency, and durability of the tooling. Some common challenges include:
- Material selection: Choosing the right material for the tooling can be a challenge, as it depends on the application, material being molded, and desired performance.
- Design complexity: Complex tooling designs can be difficult and expensive to produce, requiring specialized machining techniques and frequent testing and validation.
- Manufacturing tolerance: The precision and tolerances required in tooling production can be challenging to achieve, as small variations can affect the performance and quality of the final product.
- Lead time: The time required to produce tooling can be a significant challenge, as it can impact production schedules and time-to-market for new products.
- Cost: Tooling production can be costly, requiring significant investments in equipment, materials, and labor.
-
4.Injection Molding Tool Maintenance
Importance of Tool Maintenance:
Regular maintenance of injection molding tooling is essential to ensure its longevity, prevent defects and delays in production, and reduce costs associated with frequent repairs or replacement. Proper maintenance can minimize downtime, maintain optimal tool performance, and ultimately extend the life of the tooling.
Common Tooling Maintenance Procedures:
The following are some common maintenance procedures for injection molding tooling:
- Cleaning: removing plastic residue, dirt, and debris from the tooling surface using specialized cleaning solutions, brushes, and tools.
- Lubrication: applying a thin layer of lubricant to the tooling surface to minimize friction and wear and keep the tooling running smoothly.
- Inspection: regularly checking the tooling for signs of damage or wear, such as cracks, nicks, or wear marks.
- Reconditioning: fixing or repairing any damage or wear, such as replacing worn-out components or repairing cracks or nicks, to ensure the integrity of the tooling.
- Storage: storing the tooling in a secure location, protected from moisture, heat, and other environmental conditions, to prevent rust and other types of damage.
Extending Tool Life:
Proper maintenance and care can extend the life of injection molding tooling. Some strategies to extend the tool life include:
- Material selection: choosing durable and wear-resistant tooling materials, such as beryllium copper, can improve the longevity of the tooling.
- Cooling system optimization: optimizing the cooling system to maintain consistent temperatures and minimize thermal stresses can reduce wear and extend the tool life.
- Reducing cycle time: reducing the cycle time can minimize wear and stress on the tooling, extending its life.
- Preventive maintenance: implementing routine and preventive maintenance procedures can help detect and prevent damage or wear before it becomes significant, reducing repair costs and prolonging tool life.
- Proper handling and storage: handling and storing the tooling correctly can prevent damage or corrosion and extend its life.
-
5.Injection Molding Tool Optimization
Tooling Optimization Techniques:
The optimization of injection molding tooling is a continuous process aimed at improving its performance, efficiency, and quality. Some common tooling optimization techniques include:
- Design optimization: optimizing the tooling design to reduce material usage, minimize part distortion or warpage, and improve process consistency and repeatability.
- Cooling system optimization: optimizing the cooling system to minimize cycle time, reduce thermal stresses, and improve part quality and consistency.
- Process parameter optimization: optimizing the processing parameters, such as temperature, pressure, and injection speed, to achieve optimal part quality, cycle time, and material usage.
- Tool coatings and surface treatments: applying specialized coatings or surface treatments to the tooling surface can improve release properties, minimize wear, and reduce friction.
Reducing Cycle Time:
Reducing cycle time is a crucial aspect of injection molding tool optimization, as it can improve production efficiency and reduce costs. Some ways to reduce cycle time include:
- Optimizing the cooling system: as mentioned, optimizing the cooling system can significantly reduce cycle time by ensuring consistent cooling and minimizing thermal stresses.
- Reducing the injection molding machine idle time: using a high-speed injection molding machine, optimizing the clamp tonnage, and reducing the machine idle time can save time and improve production efficiency.
- Cavity fill optimization: optimizing the cavity fill by adjusting the injection speed, pressure, and holding time can reduce cycle time without affecting part quality.
Reducing Scrap Rates:
Reducing scrap rates is another crucial aspect of injection molding tool optimization, as it can minimize waste and improve production efficiency. Some strategies to reduce scrap rates include:
- Process parameter optimization: as mentioned earlier, optimizing the process parameters can improve part quality and consistency, reducing the likelihood of scrap.
- Proper tool maintenance: maintaining the tooling in optimal condition can prevent defects and damage that can lead to scrap.
- Process monitoring and control: monitoring the production process parameters, such as temperature and pressure, and implementing real-time process control can prevent process deviations that can lead to scrap.
Tooling Modifications and Improvements:
Modification or improvement of injection molding tooling can improve productivity, quality, and costs. Some ways of improving the tooling include:
- Changing the gate location to optimize part quality or reduce cycle time
- Implementing a more efficient cooling system to reduce cycle time
- Adopting hot runner mold technology to reduce scrap rates and waste material
- Upgrading the tooling for multi-cavity mold technology to increase production efficiency
- Implementing automation solutions such as robotics and smart sensors to minimize downtime and improve productivity.
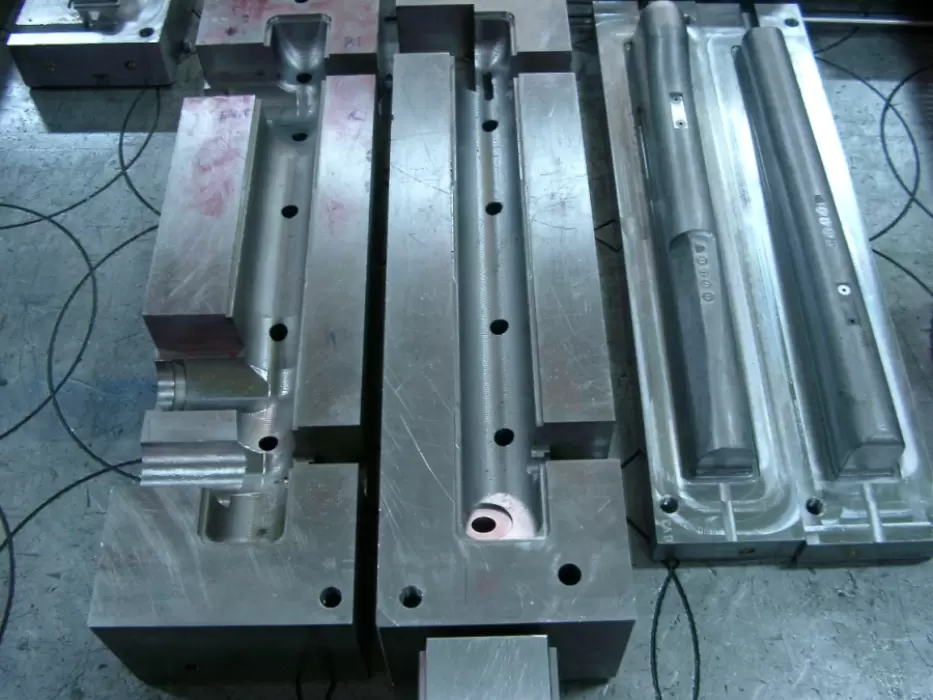
-
6.Injection Molding Tooling Costs
Factors Affecting Tooling Costs:
Injection molding tooling costs can vary significantly depending on several factors, including:
- Part size and complexity: larger or more complex parts require more extensive and sophisticated tooling, increasing costs.
- Material selection: the cost of the tooling material can vary significantly, depending on its properties and availability.
- Tooling design: more complex tooling designs require specialized techniques, increasing the cost of fabrication.
- Production volume: lower volumes typically require less expensive tooling, while higher volumes require more durable and longer-lasting tooling, which can increase costs.
- Lead time: faster tooling production timelines often require additional resources, increasing the overall cost.
Tooling Cost Estimation:
Estimating injection molding tooling costs involves several factors, such as:
- Design complexity: complex designs require more extensive machining, adding to the cost of tooling.
- Material cost: the material used to produce the tooling significantly impacts the cost.
- Tooling size and configuration: larger or more extensive tooling requires more material and labor, increasing the overall cost.
- Manufacturing processes: various manufacturing processes, such as machining, welding, or polishing, impact the overall cost.
Reducing Injection Molding Tooling Costs:
Some ways to reduce injection molding tooling costs include:
- Simplifying part design: simpler part designs require less complex tooling, reducing costs.
- Cost-effective material selection: choosing less expensive materials can reduce overall tooling costs.
- Tooling optimization: optimizing tooling design, cooling systems, and processing parameters can reduce production costs.
- Multi-cavity mold technology: using multi-cavity molds can reduce tooling costs, as it allows production of multiple parts simultaneously using one mold.
- Collaboration with the manufacturer: collaborating with the tooling manufacturer to find cost-effective solutions while ensuring that the tooling meets the necessary requirements can significantly reduce costs.
-
7.Conclusion
Injection molding tooling production and optimization are essential aspects of the injection molding process. The production of high-quality and durable tooling that can withstand the stresses and demands of production is crucial to achieving consistent and efficient production runs. Optimizing tooling design, cooling systems, and processing parameters can improve production efficiency, reduce cycle times, and minimize scrap rates.
Key Takeaways:
- Injection molding tooling production involves several stages, including design, fabrication, validation, and testing.
- Proper maintenance and care can extend the life of injection molding tooling.
- Optimizing tooling design, cooling systems, and processing parameters can improve production efficiency, reduce cycle times, and minimize scrap rates.
- Factors affecting injection molding tooling costs include part size and complexity, material selection, tooling design, production volume, and lead time.
- Strategies for reducing injection molding tooling costs include simplifying part design, cost-effective material selection, tooling optimization, multi-cavity mold technology, and collaborating with the tooling manufacturer.
Further Reading and Resources:
- Injection Molding Handbook by D.V. Rosato, M.J. Rosato, and M.B. Rosato
- Injection Molding: An Introduction by Walter Michaeli
- Moldflow Design Guide: A Resource for Plastics Engineers by Jay Shoemaker and Paul Fong
- Plastics Technology: Injection Molding Tooling Design Basics by Randy Kerkstra (https://www.ptonline.com/articles/injection-molding-tooling-design-basics)